What's a Steel Flange and Why Do You Need It?
Steel flanges are essential connecting components in piping systems that enable secure joining of pipes, valves, pumps and other equipment while allowing for maintenance access. These circular discs with evenly spaced bolt holes create strong, leak-proof connections that can withstand high pressures and temperatures in industrial applications. Steel flanges come in various materials (carbon steel, stainless steel, alloy) and designs to accommodate different system requirements - from simple water pipelines to complex chemical processing plants. Understanding what steel flanges are and their critical functions helps engineers and project managers select the right type for their specific needs, ensuring system reliability, safety and longevity.
The Fundamental Role of Steel Flanges
Steel flanges serve multiple vital functions in piping infrastructure across industries.
Creating Secure, Maintainable Connections
The primary purpose of steel flanges is to provide strong yet removable connections between piping components. Unlike permanent welded joints, flanged connections allow for system disassembly when maintenance, inspection or modifications are required. Steel flanges use gaskets between mating surfaces to create pressure-tight seals, with bolt tension ensuring uniform compression. This design enables easy access to valves, pumps and other equipment without requiring pipe cutting. Different flange face types (raised face, flat face, ring-type joint) are engineered for specific pressure ratings and sealing requirements, making steel flanges versatile solutions for diverse operating conditions.
Accommodating System Expansion and Flexibility
Steel flanges provide inherent flexibility in piping system design and future expansion. Their modular nature allows engineers to plan for potential system modifications by including flanged connections at strategic locations. This proves particularly valuable in industrial plants where process changes are common. Expansion joint flanges with flexible elements can absorb thermal movement in high-temperature pipelines, while vibration-isolating flange designs help dampen mechanical vibrations in pump and compressor systems. The ability to easily disconnect and reconnect piping sections makes steel flanges indispensable in facilities requiring operational flexibility.
Ensuring Safety Under Extreme Conditions
In high-pressure and high-temperature applications, properly specified steel flanges maintain system integrity under demanding operating conditions. Their robust construction and precise engineering prevent catastrophic failures that could lead to leaks, spills or explosions. Specialized flange designs like weld neck types provide reinforcement in critical services, while proper material selection ensures compatibility with corrosive or hazardous media. The bolted connection design of steel flanges allows for controlled assembly and disassembly procedures, reducing risks during maintenance operations compared to welded alternatives.
Popular Steel Flange Types
Different flange designs serve specific purposes in piping systems.
Weld Neck Flanges for Critical Services
Weld neck steel flanges feature a long tapered hub that provides reinforcement in high-stress applications. The smooth transition from flange thickness to pipe wall minimizes stress concentrations, making them ideal for extreme pressure and temperature conditions. These steel flanges are butt-welded to the pipe, creating the strongest possible connection suitable for refinery piping, power plants and high-pressure steam systems. Their extended neck allows for radiographic inspection of the weld joint, a critical requirement in regulated industries. Weld neck steel flanges are typically specified for systems above Class 300 rating or where cyclic loading is expected.
Slip-On Flanges for Cost-Effective Solutions
Slip-on steel flanges offer installation advantages with their lower initial cost and simpler welding requirements. The flange slides over the pipe and is secured with two fillet welds (inside and outside), making them popular for low-to-medium pressure applications. While not as robust as weld neck varieties, slip-on steel flanges are widely used in water treatment plants, HVAC systems and general industrial applications where extreme conditions aren't a concern. Their ease of alignment during installation reduces labor costs, though proper weld penetration is essential for reliable connections. These steel flanges are commonly used in systems operating below 300 psi at moderate temperatures.
Blind Flanges for System Isolation
Blind steel flanges serve as removable closures in piping systems, allowing for future expansion or maintenance access. These solid discs without a center hole can withstand full system pressure when properly bolted, making them essential components during hydrotesting and system commissioning. In process plants, blind steel flanges safely isolate equipment for maintenance while maintaining system integrity. Special variants include spectacle blinds that combine a blind flange with a spacer ring for systems requiring periodic isolation. The thickness of blind steel flanges increases with pressure class to handle substantial internal forces across their full surface area.
Key Applications of Steel Flanges
Steel flanges are indispensable across multiple industries.
Oil and Gas Industry
The energy sector extensively uses steel flanges in both upstream and downstream operations. ANSI B16.5 Class 150 to 2500 weld neck steel flanges dominate high-pressure transmission lines, while compact flange designs with enhanced corrosion protection combat harsh environmental conditions. Offshore platforms often specify specially coated steel flanges to withstand saltwater exposure, frequently combined with cathodic protection systems. The industry increasingly uses low-temperature tested steel flanges for arctic applications where material toughness at sub-zero temperatures is critical for operational safety and reliability.
Water and Wastewater Systems
Municipal water systems commonly use steel flanges for large-diameter transmission mains and treatment plant piping. Cement-lined ductile iron flanges handle potable water systems, while rubber-gasket joints with grooved steel flanges simplify installation in treatment plants. For corrosive wastewater applications, epoxy-coated or stainless-steel clad carbon steel flanges provide cost-effective solutions. Engineers frequently specify restrained joint steel flanges in seismic zones where maintaining pipeline integrity during ground movement is essential for public safety and system reliability.
Chemical and Power Plants
Chemical processing facilities rely on steel flanges to handle aggressive media at various temperatures and pressures. Alloy steel flanges resist corrosion from acids and caustics, while specialized gasket materials prevent chemical degradation. Power plants use steel flanges throughout steam and cooling water systems, with material selection based on temperature ranges and pressure requirements. Proper flange specification is critical in these industries to prevent leaks of hazardous substances and ensure continuous plant operation.
Conclusion
Steel flanges are far more than simple connectors - they are engineered components vital to piping system integrity, safety and maintainability. Understanding their types, functions and proper application ensures reliable performance across industrial sectors. From enabling equipment maintenance to withstanding extreme pressures, steel flanges play a crucial role in modern infrastructure.
HEBEI RAYOUNG PIPELINE:Your Trusted Steel Flange Manufacturer
HEBEI RAYOUNG PIPELINE TECHNOLOGY CO., LTD specializes in manufacturing high-quality steel flanges that meet international standards including ANSI, ASME, and DIN specifications. Our ISO 9001:2015 certified production facility delivers reliable flange solutions for oil & gas, water treatment, and industrial applications. With GOST-R and SGS certifications ensuring quality, we provide weld neck, slip-on, blind and specialty steel flanges in various materials and sizes.
Contact our experts today at info@hb-steel.com to discuss your project requirements and discover how our steel flange solutions can enhance your piping system's performance and reliability.
References
1. ASME B16.5 - Pipe Flanges and Flanged Fittings
2. ASME B16.47 - Large Diameter Steel Flanges
3. API 6A - Specification for Wellhead Equipment
4. EN 1092-1 - Flanges and their joints
5. MSS SP-44 - Steel Pipeline Flanges
6. ASME Boiler and Pressure Vessel Code, Section VIII
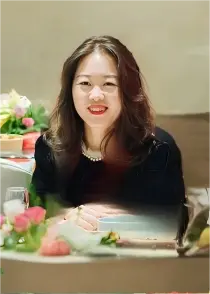
Need a quote? Want to see samples? Just say hello. We’re friendly. We’re fast. And we’re ready when you are.
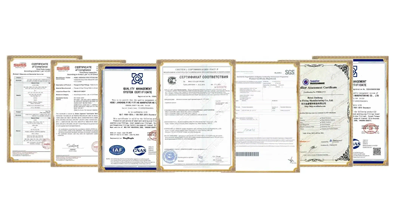
Welcome to RAYOUNG – Strong Pipes, Stronger Promise