Pipe Coating Technologies: FBE vs 3LPE vs CWC for Underground and Subsea Applications
The selection of appropriate coating technologies for steel pipes represents a critical decision in pipeline infrastructure development, particularly for underground and subsea applications where environmental challenges demand superior protection systems. Modern pipeline projects require comprehensive understanding of three primary coating methodologies: Fusion Bonded Epoxy (FBE), Three Layer Polyethylene (3LPE), and Cold Water Coating (CWC) systems.
Each technology offers distinct advantages in corrosion resistance, mechanical protection, and long-term durability for steel pipes operating in harsh environments. The choice between these coating systems depends on various factors including operating temperatures, soil conditions, installation methods, and project-specific requirements that influence pipeline performance and lifecycle costs.
Understanding Fusion Bonded Epoxy (FBE) Coating Systems
Chemical Composition and Application Process
Fusion Bonded Epoxy represents a thermosetting polymer coating system specifically engineered for steel pipes requiring exceptional corrosion protection in underground environments. The coating process involves heating steel pipes to temperatures between 180-250°C, followed by electrostatic application of epoxy powder that chemically bonds with the pipe surface upon cooling. This creates a seamless, pin-hole free barrier that effectively prevents moisture penetration and electrochemical corrosion. The molecular structure of FBE coatings provides excellent adhesion properties, ensuring long-term performance even under challenging soil conditions. Modern FBE formulations incorporate advanced additives including flow control agents, degassing compounds, and thermal stabilizers that enhance coating uniformity and extend service life for steel pipes in critical infrastructure applications.
Performance Characteristics in Underground Applications
The performance of FBE-coated steel pipes in underground environments demonstrates superior resistance to cathodic disbondment, chemical attack, and mechanical damage during installation. Laboratory testing indicates that properly applied FBE coatings maintain their protective properties for decades under normal operating conditions, with minimal degradation in adhesion strength or barrier effectiveness. The coating's inherent flexibility allows accommodation of thermal expansion and contraction cycles without cracking or delamination, making it particularly suitable for steel pipes in temperature-variable environments. Field experience confirms that FBE systems provide excellent protection against soil-based corrosion mechanisms, including bacterial activity and chemical aggression from groundwater contaminants. The coating's dielectric properties also contribute to the effectiveness of cathodic protection systems, reducing current requirements and improving overall pipeline protection strategies.
Limitations and Considerations for Steel Pipes
Despite its advantages, FBE coating systems present certain limitations that must be considered during steel pipes selection and design phases. The coating's susceptibility to damage from impact and abrasion during handling and installation requires careful construction practices and protective measures. Temperature limitations restrict FBE applications to operating temperatures below 80°C, making it unsuitable for high-temperature pipeline systems. The coating's thickness, typically ranging from 300-500 microns, provides adequate protection but may require additional mechanical protection in rocky or aggressive soil conditions. Field repairs of damaged FBE coatings require specialized equipment and skilled technicians, potentially increasing maintenance costs over the pipeline's operational life. Additionally, the coating's performance can be affected by poor surface preparation or application conditions, emphasizing the importance of quality control throughout the coating process for steel pipes.
Three Layer Polyethylene (3LPE) Coating Technology
System Architecture and Manufacturing Process
Three Layer Polyethylene coating represents an advanced protection system combining the corrosion resistance of epoxy with the mechanical strength of polyethylene for steel pipes in demanding applications. The system consists of a fusion bonded epoxy primer layer, an adhesive copolymer intermediate layer, and a polyethylene topcoat that provides comprehensive protection against environmental challenges. The manufacturing process begins with steel pipes surface preparation through shot blasting, followed by sequential application of each layer using specialized equipment that ensures proper adhesion and uniform thickness. The epoxy primer layer, typically 80-120 microns thick, provides primary corrosion protection and serves as the foundation for subsequent layers. The adhesive layer, usually 170-250 microns, ensures strong interlayer bonding, while the polyethylene topcoat, ranging from 1.8-3.2mm, delivers mechanical protection and chemical resistance for steel pipes in aggressive environments.
Enhanced Protection for Subsea Applications
The multi-layer architecture of 3LPE coatings provides exceptional protection for steel pipes in subsea environments where hydrostatic pressure, seawater corrosion, and mechanical stresses present unique challenges. The system's design philosophy addresses multiple failure modes simultaneously, with each layer contributing specific protective functions that enhance overall system reliability. The polyethylene topcoat offers superior impact resistance and flexibility, accommodating pipeline movements during installation and operation without compromising coating integrity. Subsea applications benefit from the coating's excellent water absorption resistance and long-term stability under constant immersion conditions. The system's thermal properties allow operation at elevated temperatures while maintaining protective effectiveness, making it suitable for steel pipes in offshore oil and gas production systems where thermal cycling and pressure variations are common operational conditions.
Installation and Long-term Performance
The installation of 3LPE-coated steel pipes requires specialized handling techniques and equipment to prevent coating damage during transportation and laying operations. The coating's robust construction provides excellent resistance to installation stresses, including bending, pulling, and contact with installation vessels or seabed conditions. Long-term performance data demonstrates that properly applied 3LPE systems maintain their protective properties for decades under normal operating conditions, with minimal degradation in adhesion or barrier effectiveness. The coating's resistance to cathodic disbondment ensures compatibility with cathodic protection systems, providing enhanced corrosion protection for steel pipes in marine environments. Field experience indicates that 3LPE-coated pipelines exhibit low failure rates and extended service life, making them cost-effective solutions for critical infrastructure projects. The system's repairability allows for localized maintenance without affecting overall pipeline integrity, supporting long-term operational efficiency.
Cold Water Coating (CWC) Systems and Applications
Technology Overview and Application Methods
Cold Water Coating systems represent specialized protection solutions designed for steel pipes requiring rapid application and cure capabilities in challenging environmental conditions. These systems utilize advanced polymer technologies that achieve full cure at ambient temperatures, eliminating the need for thermal processing and reducing energy requirements during application. The coating process involves surface preparation of steel pipes through mechanical cleaning, followed by application of the coating system using conventional spray, brush, or roller techniques. CWC formulations typically incorporate epoxy, polyurethane, or hybrid polymer systems that provide excellent adhesion to steel substrates while delivering corrosion protection comparable to traditional thermal-applied coatings. The technology's flexibility allows for field application and repair capabilities, making it particularly valuable for steel pipes in remote locations or projects requiring rapid turnaround times.
Performance in Marine and Underground Environments
Cold Water Coating systems demonstrate exceptional performance characteristics in both marine and underground applications, providing reliable protection for steel pipes operating in diverse environmental conditions. The coating's chemical resistance properties protect against aggressive substances commonly encountered in industrial and marine environments, including acids, alkalis, and hydrocarbon-based fluids. Underwater cure capabilities enable application of CWC systems to steel pipes in wet conditions, expanding installation windows and reducing weather-related delays. The coating's flexibility and impact resistance provide mechanical protection during installation and operation, while maintaining excellent adhesion under cyclic loading conditions. Laboratory testing confirms that CWC systems exhibit superior resistance to cathodic disbondment and maintain their protective properties under accelerated aging conditions, ensuring long-term reliability for steel pipes in critical applications.
Advantages and Limitations in Steel Pipe Applications
The primary advantages of Cold Water Coating systems for steel pipes include rapid application and cure times, reduced energy requirements, and excellent field repair capabilities that support efficient project execution. The technology's environmental benefits, including reduced volatile organic compound emissions and energy consumption, align with modern sustainability requirements for pipeline projects. CWC systems offer cost advantages through simplified application processes and reduced equipment requirements compared to thermal-applied coatings. However, certain limitations must be considered, including thickness restrictions that may limit application to moderate corrosion environments and potential sensitivity to surface preparation quality. The coating's performance can be affected by environmental conditions during application, requiring careful timing and environmental controls to ensure optimal results. Additionally, long-term performance data for CWC systems is more limited compared to established technologies like FBE and 3LPE, requiring careful evaluation for critical steel pipes applications.
Conclusion
The selection of appropriate coating technology for steel pipes in underground and subsea applications requires careful consideration of environmental conditions, performance requirements, and project-specific factors. FBE coatings offer excellent corrosion protection for moderate environments, while 3LPE systems provide superior mechanical protection for demanding applications. Cold Water Coating systems present innovative solutions for specialized requirements, offering unique application advantages and environmental benefits for modern pipeline projects.
At HEBEI RAYOUNG PIPELINE TECHNOLOGY CO., LTD., we believe that excellent infrastructure starts with dependable materials. As one of the leading pipes and fittings manufacturers, we supply high-quality steel pipes and fittings that stand the test of time. Our expertise as a trusted steel pipes factory enables us to provide comprehensive coating solutions tailored to your specific project requirements. As leading pipes and fittings manufacturers, we understand the importance of consistent quality, ISO 9001:2015, and innovation in every application. Whether you need a reliable steel pipes supplier for underground installations or a dedicated steel pipes manufacturer for subsea projects, our team delivers professional solutions with certified materials and expedited delivery services. Contact us today as your preferred steel pipes wholesale partner to discuss your coating technology requirements and discover how our tailored solutions can enhance your pipeline infrastructure projects. Reach out to our technical team at info@hb-steel.com for expert consultation and competitive quotations.
References
1. American Petroleum Institute. (2019). Specification for Line Pipe Coatings: External Polyethylene, Polypropylene, and Polybutylene Coatings Applied by Extrusion. API Specification 5L3.
2. International Organization for Standardization. (2020). Petroleum and Natural Gas Industries - Steel Pipe for Pipeline Transportation Systems - Part 3: Coating. ISO 21809-3.
3. NACE International. (2018). External Corrosion Control of Underground or Submerged Metallic Piping Systems. NACE SP0169.
4. European Committee for Standardization. (2021). Petroleum and Natural Gas Industries - External Coatings for Buried or Submerged Pipelines Used in Pipeline Transportation Systems. EN 12068.
5. DNV GL. (2017). Submarine Pipeline Systems - Recommended Practice for Design, Installation, and Operation. DNV-RP-F101.
6. American Society for Testing and Materials. (2019). Standard Practice for Application of Fusion-Bonded Epoxy Coating to Steel Pipe. ASTM D3964.
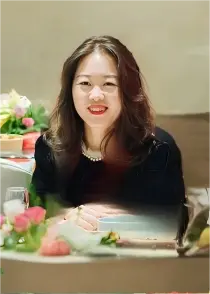
Need a quote? Want to see samples? Just say hello. We’re friendly. We’re fast. And we’re ready when you are.
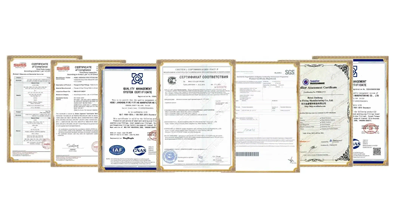
Welcome to RAYOUNG – Strong Pipes, Stronger Promise