Blind Flange Calculations: How to Determine Minimum Thickness for Safety Compliance?
In industrial piping systems, determining the proper thickness of blind flanges is crucial for maintaining safety standards and ensuring operational reliability. Blind flanges serve as essential components that seal pipeline terminals, pressure vessels, and valves, effectively blocking fluid flow while withstanding significant mechanical stress. Understanding the calculation methods for minimum thickness requirements is fundamental for engineers, project managers, and procurement specialists working with steel pipe flanges and related components. When calculating minimum thickness for blind flanges, engineers must consider multiple factors including system pressure, material properties, flange dimensions, and safety factors. The process involves applying established engineering formulas that account for the unique stress distribution patterns in blind flanges, which differ significantly from other flange types due to their solid construction without center holes. These calculations ensure that the selected blind flanges can withstand both the internal pressure forces and the bolting forces required for proper installation, while maintaining compliance with industry standards such as ASME B16.5 and relevant safety codes.
Understanding Pressure-Based Thickness Calculations for Blind Flanges
Material Properties and Stress Analysis in Steel Pipe Flanges
The foundation of blind flange thickness calculations begins with understanding the material properties and stress distribution patterns unique to these components. Steel pipe flanges, particularly blind flanges, experience complex stress patterns that require careful analysis to ensure structural integrity. The material's allowable stress values, typically derived from ASME standards, serve as the baseline for all calculations. For carbon steel blind flanges, the allowable stress varies with temperature and must be adjusted accordingly for specific operating conditions.
The stress analysis involves evaluating both radial and tangential stresses that develop within the flange body when subjected to internal pressure. Unlike standard flanges with center holes, blind flanges experience maximum stress at the center of the disc, creating a unique stress distribution pattern. This pattern requires engineers to consider the flange as a circular plate fixed at its outer edge, with uniform pressure loading across its surface. The calculation must account for the material's yield strength, ultimate tensile strength, and appropriate safety factors to ensure reliable performance under all operating conditions.
Pressure Rating Systems and Design Parameters
Modern blind flange thickness calculations rely on established pressure rating systems that categorize flanges based on their pressure-handling capabilities. The ASME B16.5 standard defines pressure classes including 150#, 300#, 600#, 900#, 1500#, and 2500#, each corresponding to specific pressure ratings at different temperatures. These ratings directly influence the required minimum thickness for blind flanges, as higher pressure classes demand thicker flange bodies to maintain structural integrity.
The design parameters for blind flange calculations include the flange's outer diameter, bolt circle diameter, and the specific pressure rating requirements. Engineers must also consider the flange face type, whether raised face (RF), flat face (FF), or ring type joint (RTJ), as each configuration affects the stress distribution and required thickness. The calculation process involves determining the effective pressure area, which differs from the nominal pipe size due to the flange's geometric configuration. This effective area, combined with the design pressure and appropriate safety factors, determines the minimum thickness required for safe operation.
Safety Factors and Code Compliance Requirements
Safety factors play a critical role in blind flange thickness calculations, ensuring that the component can handle unexpected pressure surges, temperature variations, and long-term material degradation. Standard safety factors typically range from 2.5 to 4.0, depending on the specific application and governing codes. These factors account for uncertainties in material properties, manufacturing tolerances, and operating conditions that may exceed design parameters.
Code compliance requirements mandate that all blind flange calculations follow established engineering standards and undergo proper verification procedures. The ASME Boiler and Pressure Vessel Code provides comprehensive guidelines for pressure vessel components, including blind flanges used in various applications. Engineers must ensure that their calculations comply with relevant sections of these codes, particularly Section VIII for pressure vessels and Section B31 for piping systems. The verification process includes stress analysis, fatigue evaluation, and documentation requirements that demonstrate compliance with safety standards.
Mechanical Stress Considerations and Bolting Forces
Bolt Load Distribution and Flange Deformation
The mechanical stress analysis of blind flanges extends beyond pressure considerations to include the effects of bolting forces and their distribution around the flange perimeter. When blind flanges are installed, the bolt preload creates additional stresses that must be superimposed on the pressure-induced stresses. This combination can result in complex stress patterns that require careful evaluation to prevent flange failure or leakage.
The bolting force distribution depends on the number of bolts, their size, and the bolt circle diameter. Each bolt contributes to the overall clamping force that keeps the flange assembly sealed, but uneven bolt loading can create stress concentrations that compromise the flange's integrity. Engineers must calculate the required bolt load based on the flange's pressure rating and gasket requirements, then verify that the resulting stresses remain within acceptable limits for the flange material and thickness.
Thermal Stress Effects on Steel Pipe Flanges
Temperature variations in operating conditions introduce thermal stresses that can significantly impact blind flange performance. Steel pipe flanges experience thermal expansion and contraction that creates additional stresses beyond those from pressure and bolting forces. These thermal stresses can be particularly problematic in applications with frequent temperature cycling or extreme temperature conditions.
The thermal stress calculation involves determining the temperature difference between the flange body and the surrounding structure, then applying appropriate thermal expansion coefficients for the steel material. Blind flanges, due to their solid construction, may experience different thermal expansion rates compared to the connected piping, creating interface stresses that must be considered in the overall design. The thickness calculation must account for these thermal effects to ensure that the combined stresses remain within acceptable limits throughout the operating temperature range.
Dynamic Loading and Fatigue Analysis
Industrial applications often subject blind flanges to dynamic loading conditions that can cause fatigue failures over time. These dynamic loads may result from pressure fluctuations, vibration, thermal cycling, or equipment operation. The fatigue analysis requires understanding the magnitude and frequency of these dynamic loads to predict the flange's service life and ensure adequate thickness for long-term reliability.
The fatigue evaluation process involves determining the stress range experienced by the flange during normal operation, then comparing this range to the material's fatigue strength curves. Blind flanges may be particularly susceptible to fatigue cracking at stress concentration points, such as the transition between the flange body and the raised face. The thickness calculation must incorporate appropriate fatigue factors to ensure that the flange can withstand the expected number of load cycles throughout its design life.
Standard Calculations and Industry Best Practices
ASME B16.5 Calculation Methods
The ASME B16.5 standard provides the fundamental calculation methods for determining blind flange thickness requirements. These calculations are based on classical plate theory, treating the blind flange as a circular plate with fixed edges subjected to uniform pressure loading. The standard formula considers the flange's effective diameter, design pressure, material allowable stress, and appropriate safety factors to determine the minimum required thickness.
The calculation process begins with establishing the flange's dimensions and operating conditions, then applying the appropriate formula based on the flange type and pressure rating. For blind flanges, the calculation must account for the absence of a center hole, which affects the stress distribution compared to standard flanges. The ASME B16.5 method provides tables and charts that simplify the calculation process while ensuring compliance with established safety standards.
Quality Control and Manufacturing Tolerances
Manufacturing quality control plays a crucial role in ensuring that blind flanges meet the calculated thickness requirements. Steel pipe flanges manufacturers must maintain strict tolerances during production to ensure that the actual thickness matches the design specifications. Quality control procedures include material testing, dimensional verification, and surface finish inspection to guarantee that each flange meets the required standards.
The manufacturing process for blind flanges involves several steps that can affect the final thickness, including forging, machining, and heat treatment. Each step must be carefully controlled to maintain the required dimensions and material properties. Quality control measures include ultrasonic testing to verify thickness uniformity, hardness testing to confirm proper heat treatment, and dimensional inspection to ensure compliance with drawing specifications.
Testing and Verification Procedures
Comprehensive testing and verification procedures are essential for confirming that blind flanges meet their design requirements. These procedures include hydrostatic testing to verify pressure-handling capability, dimensional inspection to confirm geometric accuracy, and material testing to validate mechanical properties. The testing process must be conducted according to established standards and documented to provide traceability for quality assurance purposes.
The verification process extends beyond individual flange testing to include assembly verification and system integration testing. Blind flanges must be tested in their actual service configuration to ensure that the calculated thickness provides adequate performance under real operating conditions. This testing may include pressure cycling, temperature exposure, and long-term monitoring to validate the design calculations and ensure reliable operation throughout the flange's service life.
Conclusion
Determining the minimum thickness for blind flanges requires a comprehensive understanding of pressure calculations, mechanical stress analysis, and industry standards. The calculation process must consider multiple factors including material properties, pressure ratings, bolting forces, thermal effects, and fatigue requirements to ensure safe and reliable operation. By following established calculation methods and industry best practices, engineers can specify blind flanges that meet safety compliance requirements while providing long-term reliability in demanding industrial applications.
At HEBEI RAYOUNG PIPELINE TECHNOLOGY CO., LTD., we believe that excellent infrastructure starts with dependable materials. As one of the leading pipes and fittings manufacturers, we supply high-quality steel pipes and fittings that stand the test of time. Our expertise as a premier steel pipe flanges factory ensures that every blind flange meets the highest standards for thickness calculations and safety compliance. As a trusted supplier and blind flanges manufacturer, we provide comprehensive support for your project requirements, from initial design calculations to final delivery. Our steel pipe flanges wholesale operations serve contractors and industrial developers worldwide with certified materials that exceed expectations. For expert guidance on blind flange calculations and customized solutions, contact our engineering team at info@hb-steel.com.
References
1. American Society of Mechanical Engineers. "Pipe Flanges and Flanged Fittings: NPS 1/2 Through NPS 24 Metric/Inch Standard." ASME B16.5-2020.
2. Harvey, J.F. "Theory and Design of Pressure Vessels." 2nd Edition, Van Nostrand Reinhold, New York, 1985.
3. Jawad, M.H. and Farr, J.R. "Structural Analysis and Design of Process Equipment." 3rd Edition, Wiley, New York, 2019.
4. Bickford, J.H. "Gaskets and Gasketed Joints." 2nd Edition, Marcel Dekker, New York, 1998.
5. Singh, K.P. and Soler, A.I. "Mechanical Design of Heat Exchangers and Pressure Vessel Components." Arcturus Publishers, Cherry Hill, New Jersey, 1984.
6. Brownell, L.E. and Young, E.H. "Process Equipment Design: Vessel Design." John Wiley & Sons, New York, 1959.
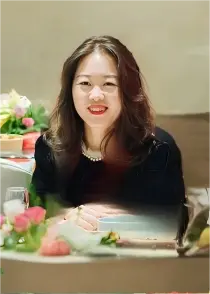
Need a quote? Want to see samples? Just say hello. We’re friendly. We’re fast. And we’re ready when you are.
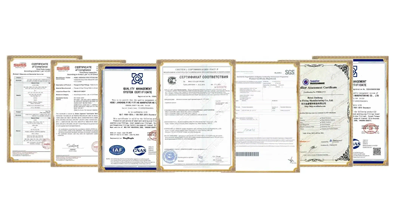
Welcome to RAYOUNG – Strong Pipes, Stronger Promise