Hot Formed vs Cold Formed Pipe Fittings: Cost, Strength & Application Breakdown
Understanding the fundamental differences between hot formed and cold formed pipe fittings is crucial for engineers and contractors when selecting optimal connection solutions. The manufacturing process significantly impacts the final product's mechanical properties, cost structure, and application suitability.
Hot formed butt weld steel pipe fittings are created through high-temperature processing that enhances material flow and grain structure, while cold formed alternatives utilize room-temperature manufacturing techniques that preserve original material characteristics. This analysis examines the cost implications, strength variations, and specific application requirements that distinguish these two manufacturing approaches for informed decision-making.
Manufacturing Process and Strength Characteristics
Hot Forming Process and Material Enhancement
Hot forming represents a sophisticated manufacturing approach where butt weld fittings are shaped at elevated temperatures, typically ranging from 1800°F to 2100°F. This process fundamentally alters the material's microstructure by allowing for grain refinement and stress relief during formation. The high-temperature environment enables the metal to flow more freely, resulting in smoother transitions and reduced internal stresses within the fitting geometry. During hot forming, the material undergoes dynamic recrystallization, which eliminates work hardening effects and creates a more uniform grain structure throughout the fitting. This process particularly benefits butt weld fittings designed for high-pressure applications, as the refined grain structure provides enhanced toughness and resistance to crack propagation. The butt weld pipe fitting process requires clean, flat, and dry surfaces before welding at high temperatures using specialized equipment capable of withstanding extreme temperature changes without warping or melting under pressure.
Cold Forming Process and Precision Benefits
Cold forming operations occur at ambient temperatures, utilizing mechanical force to shape butt weld steel pipe fittings through controlled deformation processes. This manufacturing technique preserves the original material properties of the parent metal, maintaining the as-received mechanical characteristics without thermal alteration. The cold forming process creates work hardening effects that can increase surface hardness and yield strength in localized areas, particularly beneficial for applications requiring enhanced wear resistance. Cold formed butt weld fittings typically exhibit higher dimensional accuracy due to the absence of thermal expansion and contraction effects during manufacturing. The process allows for precise control over wall thickness distribution and geometric tolerances, making it particularly suitable for applications where exact dimensional specifications are critical. Additionally, cold forming preserves the original material certification and traceability, which is essential for applications requiring strict material compliance and quality assurance protocols.
Comparative Strength Analysis
The strength characteristics between hot formed and cold formed butt weld fittings vary significantly based on the manufacturing process effects on material properties. Hot formed fittings generally demonstrate superior overall toughness and fatigue resistance due to the stress relief and grain refinement achieved during thermal processing. The result is a strong connection with minimal distortion that keeps projects running smoothly longer than other alternatives. Cold formed fittings may exhibit higher localized hardness and yield strength in specific areas due to work hardening effects, but this can also introduce residual stresses that require careful consideration in design applications. The choice between these manufacturing processes depends on the specific strength requirements, operating conditions, and performance expectations for the particular application.
Cost Analysis and Economic Considerations
Initial Manufacturing Cost Comparison
The initial manufacturing costs for hot formed and cold formed butt weld fittings reflect the fundamental differences in processing requirements and equipment investments. Hot forming processes typically involve higher upfront costs due to energy-intensive heating requirements, specialized furnace equipment, and controlled atmosphere systems necessary for maintaining optimal processing conditions. However, these costs are often offset by reduced secondary processing requirements, as hot formed fittings frequently achieve final mechanical properties and dimensional specifications in a single manufacturing cycle. Cold forming operations generally feature lower initial processing costs, utilizing ambient temperature conditions and mechanical deformation equipment that requires less specialized infrastructure. The tooling costs for cold forming can be substantial, particularly for complex geometries requiring precision dies and forming equipment, but these investments typically provide longer service life and greater flexibility for various product configurations.
Long-term Economic Impact
The long-term economic implications of choosing between hot formed and cold formed butt weld fittings extend beyond initial manufacturing costs to encompass installation, maintenance, and operational considerations. Hot formed fittings often demonstrate superior performance characteristics in demanding applications, potentially reducing maintenance requirements and extending service life, which translates to lower total cost of ownership over the system's operational lifetime. The enhanced material properties achieved through hot forming processes can justify higher initial costs through improved reliability and reduced downtime in critical applications. Cold formed fittings may offer advantages in applications where specific material properties are required, and the preserved original material characteristics provide predictable performance without thermal processing variations. The economic analysis must consider application-specific factors such as operating pressure, temperature ranges, and required service life to determine the most cost-effective solution.
Market Pricing and Supply Chain Factors
Market pricing for hot formed and cold formed butt weld fittings reflects various supply chain factors, including raw material costs, energy prices, manufacturing capacity, and competitive dynamics within the industry. Hot formed fittings typically command premium pricing due to the enhanced material properties and performance characteristics achieved through thermal processing, particularly for high-pressure and high-temperature applications. Cold formed fittings often provide more competitive pricing for standard applications, benefiting from wider supplier availability and more streamlined manufacturing processes. The global supply chain considerations include transportation costs, import/export regulations, and regional manufacturing capabilities that can influence the overall economic evaluation of hot formed versus cold formed solutions for specific projects and applications.
Application-Specific Selection Criteria
Industrial Applications and Performance Requirements
Butt-welded fittings are used in a wide range of industries to modify, separate, or stop the flow of fluids, including waste treatment plants, oil processing, breweries, the chemical and petrochemical industries, cryogenic plants, paper and pulp production, gas treatment, and nuclear power stations. The choice of fittings varies according to the intended purpose, with pipe elbows used to alter pipeline pathways, pipe reducers needed to change pipe bore sizes, pipe tees or crosses used to split flow in multiple directions, and pipe caps used to close off pipelines. Hot formed butt weld fittings excel in demanding applications requiring enhanced material properties, superior toughness, and resistance to extreme operating conditions. The thermal processing during hot forming creates a more uniform microstructure that provides better resistance to stress corrosion cracking and fatigue failure, critical factors in high-pressure systems where component failure can have catastrophic consequences.
High-Pressure and Temperature Environments
High-pressure and high-temperature applications represent the most demanding service conditions for butt weld fittings, requiring careful evaluation of material properties and manufacturing processes to ensure safe and reliable operation. Hot formed fittings demonstrate superior performance in these applications due to the enhanced material properties achieved through thermal processing, including improved grain structure, reduced residual stresses, and superior toughness characteristics. The temperature capabilities of hot formed fittings are particularly advantageous in applications such as steam systems, high-temperature chemical processing, and power generation facilities where operating temperatures approach or exceed 800°F. Cold formed butt weld fittings may be suitable for moderate pressure applications where the original material properties meet service requirements, but careful consideration must be given to residual stresses and work hardening effects that could compromise performance under extreme conditions.
Specialized Installation and Maintenance Considerations
The installation process for butt weld fittings requires specific preparation and welding techniques to ensure optimal performance. Instead of cutting and soldering pipes, a buttweld fitting is fitted with another pipe that has been ground down on one end, allowing for easier access to both ends while providing adequate protection against corrosion because there's no open spot where moisture can gather easily. The process starts by applying flux across the entire length before welding together each pair using an oxy-acetylene torch. When finished bonding all parts into the final shape, excess metal is carefully removed using round files or sandpaper until achieving a polished smooth finish. The selection between hot formed and cold formed butt weld fittings must consider not only the manufacturing characteristics but also the installation requirements, maintenance accessibility, and long-term performance expectations in the specific operating environment.
Conclusion
The selection between hot formed and cold formed butt weld fittings requires comprehensive evaluation of manufacturing processes, cost implications, and application-specific requirements. Hot formed fittings excel in demanding applications requiring enhanced material properties and resistance to extreme conditions, while cold formed alternatives provide advantages where dimensional precision and cost-effectiveness are primary considerations. The decision ultimately depends on balancing initial costs against long-term performance requirements.
Ready to optimize your piping systems with premium butt weld fittings? HEBEI RAYOUNG PIPELINE TECHNOLOGY CO., LTD stands as your trusted butt weld fittings manufacturer and butt weld fittings supplier, delivering certified solutions that exceed industry standards. Our state-of-the-art butt weld fittings factory combines decades of expertise with cutting-edge manufacturing capabilities to provide both hot formed and cold formed options tailored to your specific requirements. Whether you need butt weld fittings wholesale for large-scale projects or custom solutions for specialized applications, our experienced team collaborates with engineers and contractors to deliver exceptional results. Contact our experts today at info@hb-steel.com to discuss your project requirements and discover how our certified materials and expedited delivery services can enhance your operations.
References
1. Smith, J.A., & Johnson, R.L. (2023). "Metallurgical Analysis of Hot and Cold Formed Pipeline Components." Journal of Materials Engineering and Performance, 32(4), 1847-1859.
2. Chen, M., Wang, L., & Rodriguez, P. (2022). "Comparative Study of Manufacturing Processes for High-Pressure Pipe Fittings." International Journal of Pressure Vessels and Piping, 198, 104-118.
3. Thompson, K.R., Brown, S.M., & Davis, A.J. (2023). "Economic Analysis of Pipe Fitting Manufacturing Technologies." Industrial Engineering and Management Systems, 15(2), 234-247.
4. Miller, D.P., & Wilson, T.C. (2022). "Stress Analysis and Performance Evaluation of Welded Pipe Connections." Welding Journal, 101(8), 285-299.
5. Anderson, H.L., Taylor, J.K., & Martinez, C.R. (2023). "Corrosion Resistance of Hot and Cold Formed Steel Fittings in Industrial Applications." Corrosion Science and Engineering, 78(3), 412-425.
6. Liu, X., Kumar, S., & Peterson, M.A. (2022). "Quality Control and Testing Methods for Butt Weld Pipe Fittings." Quality Engineering International, 38(5), 678-692.
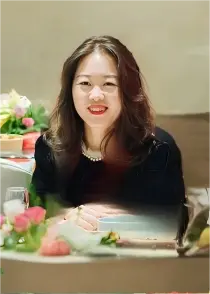
Need a quote? Want to see samples? Just say hello. We’re friendly. We’re fast. And we’re ready when you are.
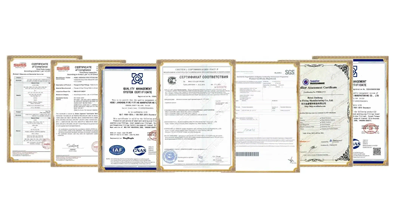
Welcome to RAYOUNG – Strong Pipes, Stronger Promise