Comprehensive Guide to Steel Pipe Flanges
Steel pipe flanges serve as the backbone of modern piping systems, providing secure connections that withstand extreme pressures and temperatures across industries. This comprehensive guide explores the essential aspects of steel pipe flanges, from their fundamental design principles to advanced application considerations. As critical components in oil and gas, chemical processing, water distribution, and power generation systems, steel pipe flanges ensure system integrity while allowing for maintenance flexibility. We'll examine the various types available, material selection criteria, and industry best practices for installation and maintenance, providing engineers and procurement specialists with the knowledge needed to make informed decisions about these vital components.
Different Steel Pipe Flange Types and Their Uses in Industry
Weld Neck Flanges for High-Pressure Systems
Weld neck flanges represent the gold standard for critical high-pressure applications due to their reinforced structural design. These steel pipe flanges feature a tapered hub that gradually transitions to the pipe wall thickness, significantly reducing stress concentrations at the joint. The extended neck provides excellent reinforcement, making them ideal for extreme temperature fluctuations and cyclic loading conditions commonly encountered in oil refineries and power plants. Their smooth bore design minimizes turbulence and erosion, particularly important for gas transmission systems where flow efficiency is paramount. The welding neck configuration also allows for easy radiographic inspection of the weld joint, a crucial factor in quality assurance for high-risk applications. Industries requiring ASME B16.5 Class 300 and above specifications typically specify weld neck steel pipe flanges for their reliability and long-term performance.
Slip-On Flanges for Cost-Effective Solutions
Slip-on steel pipe flanges offer practical advantages for low to medium pressure systems where frequent modifications may be required. Their design allows the flange to slide over the pipe before being welded in place, significantly simplifying alignment during installation compared to weld neck variants. While they lack the structural reinforcement of weld neck flanges, modern slip-on designs incorporate sufficient material thickness to handle pressures up to ASME B16.5 Class 600 in many applications. These steel pipe flanges are particularly prevalent in water treatment facilities and HVAC systems where pressure requirements are moderate but installation speed is crucial. The reduced hub height also makes them suitable for space-constrained installations, though engineers must carefully consider the double-welding requirement (inside and outside the flange) when specifying them for critical services.
Blind Flanges for System Isolation and Testing
Blind steel pipe flanges serve as permanent or temporary end closures in piping systems, playing vital roles in maintenance, testing, and future expansion planning. Unlike other flange types, blind flanges don't have a center bore, allowing them to completely seal off pipe ends during pressure testing or system modifications. Their solid plate construction makes them exceptionally robust, capable of withstanding the full pressure rating of the flange class without leakage concerns. In petrochemical plants, blind flanges are routinely used for safe isolation of equipment during turnaround operations. Modern designs often incorporate lifting lugs or handling holes to facilitate installation and removal of these heavy components. When selecting blind steel pipe flanges, engineers must pay particular attention to material compatibility with the connected piping system to prevent galvanic corrosion issues at the mating surfaces.
Standards for Selection of Materials and Production
Carbon Steel Flanges: The Industry Workhorse
ASTM A105 carbon steel flanges dominate industrial applications due to their optimal balance of strength, weldability, and cost-effectiveness. These steel pipe flanges undergo strict quality control during forging and machining processes to ensure dimensional accuracy and material integrity. The carbon content (typically 0.35% max) provides sufficient hardness while maintaining good ductility for flange facing machining. Normalized heat treatment refines the grain structure, enhancing mechanical properties for demanding services. For low-temperature applications down to -29°C, ASTM A350 LF2 carbon steel flanges offer improved impact resistance through controlled chemical composition and Charpy testing verification. The widespread availability of carbon steel flanges across all standard sizes and pressure ratings makes them the first choice for general industrial services where corrosion isn't a primary concern.
Stainless Steel Flanges for Corrosive Environments
Austenitic stainless steel flanges (ASTM A182 F304/F316) provide exceptional corrosion resistance for chemical processing, marine, and food-grade applications. The chromium-nickel-molybdenum alloy composition creates a passive oxide layer that resists pitting and crevice corrosion in chloride-containing environments. Duplex stainless steel flanges (ASTM A182 F51/F53) offer even greater strength and stress corrosion cracking resistance for offshore oil and gas applications. These steel pipe flanges maintain their mechanical properties across a wide temperature range while providing excellent hygienic characteristics for pharmaceutical and beverage industries. Special surface finishes (e.g., Ra < 0.8μm) can be specified for ultra-clean applications where product purity is critical. The non-magnetic nature of austenitic grades also makes them suitable for specialized applications like MRI facilities and semiconductor manufacturing.
Alloy Steel Flanges for Extreme Conditions
High-temperature alloy steel flanges (ASTM A182 F11/F22) contain chromium and molybdenum additions that provide exceptional creep resistance and oxidation protection in power generation applications. These steel pipe flanges maintain their strength at temperatures exceeding 500°C, where carbon steel would rapidly deteriorate. The alloying elements form stable carbides that prevent graphitization and maintain pressure boundary integrity over decades of service. For ultra-high pressure applications like hydraulic fracturing equipment, ASTM A694 high-yield carbon steel flanges provide the necessary strength-to-weight ratio while maintaining weldability. Special heat treatments like quenching and tempering optimize the microstructure for specific service conditions, with thorough documentation of mechanical properties and heat treatment parameters accompanying each batch of alloy steel flanges.
Top Techniques for Installation and Upkeep
Precision Alignment and Bolt Load Management
Proper installation of steel pipe flanges begins with meticulous alignment using laser measurement tools to ensure parallel flange faces and concentric bolt holes. Misalignment exceeding 0.5mm per 300mm of flange diameter can create uneven gasket compression leading to premature failure. Hydraulic bolt tensioning systems provide superior load distribution compared to traditional torque wrenches, especially for large-diameter flanges in critical services. The sequence of bolt tightening follows a star pattern to gradually compress the gasket evenly across its entire surface. Modern flange management software calculates optimal bolt loads based on gasket type, flange material, and operating conditions, replacing outdated rule-of-thumb approaches. For high-cycle fatigue applications, ultrasonic bolt load monitoring systems can verify proper preload maintenance throughout the flange's service life.
Gasket Selection and Performance Optimization
The gasket represents the weakest link in any flanged connection, making proper selection crucial for steel pipe flanges. Spiral-wound gaskets with flexible graphite filler provide excellent resilience across wide temperature ranges while maintaining sealability during pressure fluctuations. For aggressive chemical services, PTFE-enveloped gaskets offer superior chemical resistance with minimal creep relaxation. The gasket must be properly centered within the flange faces, with attention to inner diameter alignment to prevent erosion from turbulent flow. Advanced gasket seating techniques involve controlled compression in multiple stages, allowing the gasket material to flow and fill microscopic imperfections in the flange faces. Regular torque checks during the first few thermal cycles compensate for gasket relaxation, a critical step often overlooked in field installations.
Corrosion Prevention and Integrity Management
Protective coatings extend the service life of steel pipe flanges in corrosive environments, with epoxy-based systems providing excellent barrier protection for carbon steel components. Cathodic protection systems complement coatings for buried or submerged flanges in pipeline applications. Regular non-destructive testing (NDT) including ultrasonic thickness measurements and liquid penetrant inspection detects developing flaws before they compromise system integrity. For critical process piping, risk-based inspection (RBI) programs prioritize examination of flanges based on consequence of failure analysis. Advanced monitoring techniques like acoustic emission testing can detect tiny leaks in real-time, allowing for proactive maintenance before significant damage occurs. Proper documentation of each flange's service history, including pressure cycles and maintenance interventions, supports informed decision-making about replacement timing.
Conclusion
This comprehensive examination of steel pipe flanges highlights their critical role in modern industrial infrastructure. From material selection to installation best practices, understanding these components' technical nuances ensures safe, efficient, and long-lasting piping systems. The continuous evolution of flange technology, including improved materials and installation techniques, promises even greater reliability for future industrial applications.
HEBEI RAYOUNG PIPELINE: Upgrade Your Piping Systems with Premium Flange Solutions
At HEBEI RAYOUNG PIPELINE TECHNOLOGY CO., LTD, we combine decades of expertise with cutting-edge manufacturing to deliver steel pipe flanges that exceed industry standards. Our ISO 9001:2015 certified production facilities utilize advanced forging and machining technologies to create flanges with unparalleled dimensional accuracy and performance characteristics. Whether you require standard ASME B16.5 flanges or customized solutions for specialized applications, our engineering team stands ready to assist. Contact us today at info@hb-steel.com to discuss how our flange solutions can enhance your project's reliability and performance.
References
1. ASME B16.5 - Pipe Flanges and Flanged Fittings
2. ASTM A105/A105M - Standard Specification for Carbon Steel Forgings for Piping Applications
3. API 6A - Specification for Wellhead and Christmas Tree Equipment
4. MSS SP-44 - Steel Pipeline Flanges
5. EN 1092-1 - Flanges and their joints - Circular flanges for pipes, valves, fittings and accessories
6. ASME PCC-1 - Guidelines for Pressure Boundary Bolted Flange Joint Assembly
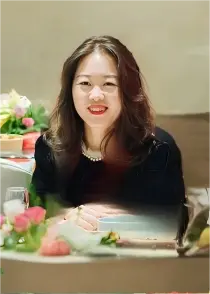
Need a quote? Want to see samples? Just say hello. We’re friendly. We’re fast. And we’re ready when you are.
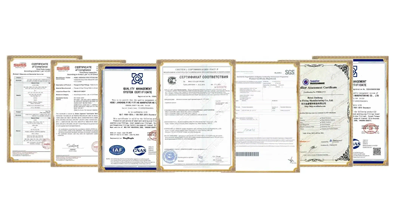
Welcome to RAYOUNG – Strong Pipes, Stronger Promise