All you need to know about Carbon Steel Flanges
Carbon steel flanges are fundamental components in piping systems across industries, providing reliable connections between pipes, valves, and equipment. These steel flanges offer an exceptional balance of strength, durability, and cost-effectiveness, making them the preferred choice for numerous applications from water distribution to oil and gas pipelines. With various types designed to meet different pressure ratings and connection requirements, carbon steel flanges ensure leak-proof performance in both low and high-pressure systems. This comprehensive guide covers everything about steel flanges - from material specifications and manufacturing processes to installation best practices and industry applications.
Types of Carbon Steel Flanges
Understanding the different flange types is essential for selecting the right connection solution for specific system requirements.
Weld Neck Flanges (WN)
Weld neck steel flanges feature a long tapered hub that provides reinforcement in high-stress applications, making them ideal for extreme pressure and temperature conditions. The smooth transition from flange thickness to pipe wall thickness significantly reduces stress concentration points. These steel flanges are butt-welded to the pipe, creating the strongest possible connection suitable for critical services like refinery piping and high-pressure steam systems. Their extended neck allows for radiographic inspection of the weld joint, a requirement in many regulated industries. Weld neck steel flanges are typically specified for systems above Class 300 rating or where cyclic loading is expected.
Slip-On Flanges (SO)
Slip-on steel flanges offer installation advantages with their lower initial cost and simpler welding requirements. The flange slides over the pipe and is secured with two fillet welds (inside and outside), making them popular for low-to-medium pressure applications. While not as robust as weld neck varieties, slip-on steel flanges are widely used in water treatment plants, HVAC systems, and general industrial applications where extreme conditions aren't a concern. Their ease of alignment during installation reduces labor costs, though engineers must ensure proper weld penetration to achieve reliable connections. These steel flanges are commonly used in systems operating below 300 psi at moderate temperatures.
Blind Flanges (BL)
Blind steel flanges serve as removable closures in piping systems, allowing for future expansion or maintenance access. These solid discs without a center hole can withstand full system pressure when properly bolted, making them essential components during hydrotesting and system commissioning. In process plants, blind steel flanges safely isolate equipment for maintenance while maintaining system integrity. Special variants include spectacle blinds that combine a blind flange with a spacer ring for systems requiring periodic isolation. The thickness of blind steel flanges increases with pressure class to handle the substantial forces exerted by internal pressure across their full surface area.
Material Specifications and Manufacturing
Carbon steel flanges are produced according to strict international standards to ensure quality and performance consistency.
ASTM A105 Standard
ASTM A105 is the most common specification for carbon steel flanges in pressure systems, covering forged components for ambient and higher-temperature service. These steel flanges contain a maximum of 0.35% carbon content, providing an optimal balance between strength and weldability. The standard requires impact testing only when specified for low-temperature applications (typically below -29°C). A105 steel flanges demonstrate excellent mechanical properties with tensile strength ranging from 485-655 MPa and minimum yield strength of 250 MPa, making them suitable for various industrial applications up to 425°C service temperature.
Forging Process and Quality Control
High-quality steel flanges are manufactured through controlled forging processes that improve grain structure and mechanical properties. The forging begins with heated carbon steel billets that are pressed into shape using hydraulic presses or hammers. This process aligns the grain flow with the flange contour, enhancing strength characteristics. Reputable manufacturers implement rigorous quality control measures including ultrasonic testing, hardness testing, and dimensional verification to ensure steel flanges meet specified requirements. Heat treatment processes like normalizing or quenching and tempering may be applied to achieve desired mechanical properties based on application needs.
Surface Treatments and Coatings
While carbon steel flanges offer excellent mechanical properties, they require proper surface protection against corrosion. Common protection methods include hot-dip galvanizing, which applies a zinc coating that sacrificially protects the base metal. For more aggressive environments, epoxy coatings or specialized paint systems provide enhanced chemical resistance. Internal protection methods for steel flanges include cement lining for water service or rubber lining for abrasive slurries. Recent advancements in metallurgical coatings, including thermal spray applications, offer improved protection with minimal dimensional impact on the flange's critical sealing surfaces.
Applications and Installation Best Practices
Proper selection and installation of carbon steel flanges are critical for long-term system reliability.
Oil and Gas Industry Applications
Carbon steel flanges are extensively used in both upstream and downstream oil and gas operations. ANSI B16.5 Class 150 to 2500 weld neck steel flanges dominate high-pressure transmission lines, while compact flange designs with enhanced corrosion protection combat harsh environmental conditions. Offshore platforms often specify specially coated steel flanges to withstand saltwater exposure, frequently combined with cathodic protection systems. The industry increasingly uses low-temperature tested carbon steel flanges for arctic applications where material toughness at sub-zero temperatures is critical for operational safety and reliability.
Water and Wastewater Systems
Municipal water systems commonly use carbon steel flanges for large-diameter transmission mains and treatment plant piping. Cement-lined ductile iron flanges handle potable water systems, while rubber-gasket joints with grooved steel flanges simplify installation in treatment plants. For corrosive wastewater applications, epoxy-coated or stainless-steel clad carbon steel flanges provide cost-effective solutions. Engineers frequently specify restrained joint steel flanges in seismic zones where maintaining pipeline integrity during ground movement is essential for public safety and system reliability.
Proper Installation Techniques
Correct installation is crucial for achieving leak-free performance from carbon steel flanges. This includes proper alignment of flange faces, selection of appropriate gasket materials, and controlled bolt tightening using calibrated torque wrenches or hydraulic tensioners. Industry standards recommend following specific tightening patterns (typically star/cross patterns) to ensure even gasket compression. Flange faces must be clean and free of damage, with surface finishes typically maintained between 125-250 microinches for raised face applications. Regular inspection and maintenance programs should include checking for bolt load retention, especially in systems experiencing thermal cycling.
Conclusion
Carbon steel flanges remain the backbone of industrial piping systems, offering reliable performance across diverse applications from municipal water to high-pressure oil and gas services. Understanding the various types, material specifications, and proper installation techniques ensures optimal selection and long-term performance of these critical components. With proper material selection and installation practices, carbon steel flanges provide decades of trouble-free service in demanding industrial environments.
HEBEI RAYOUNG PIPELINE: Your Trusted Carbon Steel Flange Manufacturer
HEBEI RAYOUNG PIPELINE TECHNOLOGY CO., LTD specializes in manufacturing high-quality carbon steel flanges that meet international standards including ANSI, ASME, and DIN specifications. Our ISO 9001:2015 certified production facility delivers reliable flange solutions for oil & gas, water treatment, and general industrial applications. With GOST-R and SGS certifications ensuring export compliance, we provide weld neck, slip-on, blind, and specialty steel flanges in various sizes and pressure ratings to meet your project requirements.
Contact our technical experts today at info@hb-steel.com to discuss your specific needs and discover how our carbon steel flange solutions can enhance your piping system's performance and durability.
References
1. ASME B16.5 - Pipe Flanges and Flanged Fittings
2. ASTM A105/A105M - Standard Specification for Carbon Steel Forgings for Piping Applications
3. ASME B16.47 - Large Diameter Steel Flanges
4. API 6A - Specification for Wellhead and Christmas Tree Equipment
5. MSS SP-44 - Steel Pipeline Flanges
6. ASME Boiler and Pressure Vessel Code, Section VIII - Pressure Vessels
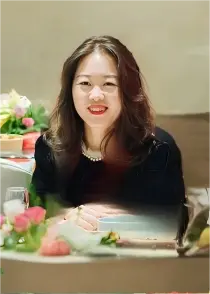
Need a quote? Want to see samples? Just say hello. We’re friendly. We’re fast. And we’re ready when you are.
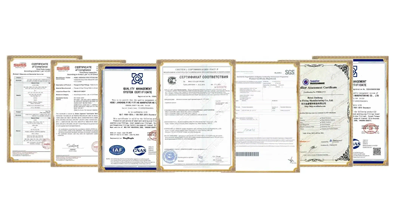
Welcome to RAYOUNG – Strong Pipes, Stronger Promise