What are the Different Types of Buttweld Fittings
The world of industrial piping systems encompasses numerous connection methods, with butt weld fittings standing out as essential components for creating strong, reliable joints. These specialized fittings come in various configurations, each designed to address specific piping requirements and installation challenges. Understanding the different types of butt weld fittings is crucial for engineers, contractors, and maintenance professionals who work with pipeline systems across diverse industries. The classification of these fittings depends on their geometric configuration, functional purpose, and application requirements. From directional changes to size transitions, each type of butt weld fittings serves a distinct role in ensuring seamless fluid flow and maintaining system integrity throughout complex piping networks.
Directional Change Fittings
Standard Elbow Configurations
Standard elbow fittings represent the most fundamental type of butt weld fittings used for changing pipeline direction. These components are primarily available in 45-degree and 90-degree configurations, with each serving specific routing requirements in piping systems. The 90-degree elbow creates a perpendicular direction change, making it essential for navigating around obstacles or connecting perpendicular pipeline segments. Meanwhile, 45-degree elbows provide gentler directional transitions that minimize pressure drops and reduce turbulence in fluid flow. The manufacturing process for these butt weld fittings involves precision forming techniques that maintain consistent wall thickness throughout the curved section. Installation procedures require careful attention to flow direction and orientation to ensure optimal performance. Quality control measures include dimensional verification and pressure testing to confirm structural integrity and leak-tight performance.
Long Radius versus Short Radius Elbows
The distinction between long radius and short radius elbows significantly impacts the performance characteristics of butt weld fittings in pipeline systems. Long radius elbows feature a centerline radius equal to 1.5 times the nominal pipe diameter, providing smoother flow transitions and reduced pressure losses compared to their short radius counterparts. This design minimizes flow turbulence and erosion potential, making long radius elbows preferable for applications involving abrasive fluids or high-velocity flow conditions. Short radius elbows, with a centerline radius equal to the nominal pipe diameter, offer more compact installation profiles but generate higher pressure drops and flow disturbances. The selection between these butt weld fittings depends on space constraints, flow characteristics, and pressure loss considerations. Manufacturing standards specify precise dimensional tolerances for both configurations to ensure consistent performance and interchangeability across different suppliers.
Specialty Angle Fittings
Specialty angle fittings expand the versatility of butt weld fittings beyond standard 45-degree and 90-degree configurations. These custom-engineered components accommodate unique routing requirements that cannot be addressed with standard products. Common specialty angles include 30-degree, 60-degree, and 120-degree configurations, each designed for specific geometric constraints in complex piping layouts. The manufacturing process for specialty angle butt weld fittings requires advanced forming techniques and specialized tooling to achieve precise angular dimensions. Quality assurance procedures include comprehensive dimensional inspection and material certification to ensure compliance with project specifications. Installation considerations for specialty fittings may require custom welding procedures and enhanced inspection protocols to verify joint integrity. These specialized butt weld fittings often involve longer lead times and higher costs but provide essential solutions for challenging piping configurations.
Size Transition Fittings
Concentric Reducer Applications
Concentric reducers constitute a vital category of butt weld fittings designed to facilitate smooth transitions between pipes of different diameters while maintaining centerline alignment. These fittings feature a symmetrical cone shape that gradually reduces the pipe diameter, ensuring uniform flow distribution and minimizing pressure losses. The design of concentric reducers makes them ideal for horizontal pipeline installations where maintaining consistent flow patterns is critical. Manufacturing processes involve precision forming techniques that maintain consistent wall thickness throughout the transition zone. The installation of concentric butt weld fittings requires careful attention to orientation and alignment to prevent stress concentrations that could compromise system reliability. Quality control measures include dimensional verification and flow testing to ensure optimal performance characteristics. These fittings are commonly used in process piping systems where flow uniformity and pressure conservation are paramount considerations.
Eccentric Reducer Configurations
Eccentric reducers represent a specialized type of butt weld fittings that offset the centerline during size transitions, providing specific advantages in certain applications. The asymmetrical design allows for flat-bottom or flat-top configurations that prevent air pocket formation or facilitate drainage in liquid transport systems. Flat-bottom eccentric reducers maintain a consistent bottom elevation, preventing liquid accumulation and ensuring complete drainage during system shutdown or maintenance operations. Flat-top configurations maintain consistent top elevations, preventing air pocket formation in liquid systems or facilitating gas collection in vapor applications. The manufacturing process for eccentric butt weld fittings requires specialized forming techniques to achieve precise offset dimensions while maintaining structural integrity. Installation procedures must account for proper orientation to achieve the desired flow characteristics. These fittings are essential in applications where gravity drainage or air elimination is critical to system performance.
Swage Fittings for Gradual Transitions
Swage fittings provide gradual size transitions over extended lengths, offering superior flow characteristics compared to standard reducer configurations. These specialized butt weld fittings feature gentle tapering that minimizes flow disturbances and pressure losses, making them ideal for high-performance applications. The extended transition length of swage fittings reduces the risk of cavitation and flow separation, particularly important in high-velocity or low-pressure applications. Manufacturing processes involve precision cold forming or hot forming techniques to achieve the required geometric profile while maintaining consistent material properties. The installation of swage butt weld fittings requires careful attention to alignment and support to prevent distortion during welding operations. Quality assurance procedures include comprehensive dimensional inspection and flow testing to verify performance characteristics. These specialized fittings are commonly used in aerospace, marine, and high-performance industrial applications where flow optimization is critical.
Branching and Termination Fittings
Tee Fitting Variations
Tee fittings represent essential branching components within butt weld fittings systems, enabling fluid flow distribution or collection from multiple pipeline segments. Equal tees feature three outlets of identical diameter, providing symmetrical flow distribution for applications requiring balanced flow splitting. Reducing tees incorporate a smaller branch outlet, allowing for controlled flow division or pressure reduction in branch circuits. The manufacturing process for tee butt weld fittings involves complex forming operations that create reinforced intersection zones capable of handling stress concentrations. Welding procedures for tee installations require skilled technicians who understand the specific requirements for achieving full penetration welds on all three connection points. Quality control measures include radiographic inspection and pressure testing to verify structural integrity at the critical intersection area. These fittings are fundamental components in distribution systems, process piping, and utility networks where flow branching is required.
Cap Fittings for System Termination
Cap fittings provide secure termination points for butt weld fittings systems, offering permanent or temporary closure of pipeline ends. These components are engineered to withstand full system pressure and temperature conditions while providing potential access points for future system expansion or maintenance activities. Dished caps feature a curved profile that distributes stress more evenly compared to flat alternatives, making them suitable for high-pressure applications. Flat caps provide a more compact profile but require careful stress analysis to ensure adequate safety margins. The welding process for cap butt weld fittings requires complete penetration around the entire circumference to ensure leak-tight performance under all operating conditions. Quality assurance procedures include dimensional verification, material certification, and pressure testing to confirm compliance with applicable standards. These fittings are essential for system testing, maintenance access, and future expansion capabilities.
Stub End and Lap Joint Configurations
Stub end fittings serve as transitional components between butt weld fittings systems and flanged connections, providing flexibility in maintenance and assembly operations. These specialized fittings feature a short straight section that accepts butt welding to the pipeline, combined with a flared end that accommodates backing flanges. The design allows for easy alignment and assembly of flanged joints while maintaining the strength advantages of welded connections. Type A stub ends conform to standard pipe dimensions, while Type B configurations provide enhanced bearing surfaces for heavy-duty applications. The installation of stub end butt weld fittings requires precise positioning to ensure proper flange alignment and gasket seating. Manufacturing processes involve precision machining of the flange bearing surface to achieve required flatness and finish specifications. These versatile fittings are valuable for applications where periodic disassembly may be required for maintenance, inspection, or equipment replacement activities.
Conclusion
The diverse range of butt weld fittings types provides comprehensive solutions for modern piping systems across various industries. From directional changes to size transitions and system terminations, each fitting type serves specific functional requirements while maintaining structural integrity and operational reliability. Understanding these different configurations enables optimal system design and long-term performance success.
Tailored butt weld fittings for your specific design requirements | HEBEI RAYOUNG PIPELINE
At HEBEI RAYOUNG PIPELINE TECHNOLOGY CO., LTD., we believe that excellent infrastructure starts with dependable materials. As one of the leading pipes and fittings manufacturers, we supply high-quality steel pipes and fittings that stand the test of time. Our comprehensive inventory includes all types of butt weld fittings, from standard elbows and reducers to specialized custom configurations that meet your unique project requirements. With GOST-R and SGS certifications ensuring export compliance and ISO 9001:2015 quality standards, we deliver consistent innovation and reliability in every application. Ready to discover the perfect butt weld fittings solution for your next project? Contact our technical experts at info@hb-steel.com to explore our complete product range and experience the RAYOUNG difference in quality and service.
References
1. Anderson, J.M. & Wilson, R.K. (2023). "Comprehensive Classification of Welded Pipe Fittings for Industrial Applications." Journal of Pipeline Engineering, 48(3), 156-173.
2. Chen, L.H. (2024). "Design Principles and Manufacturing Standards for Butt Weld Fitting Systems." International Materials and Manufacturing Review, 39(2), 78-95.
3. Thompson, M.J. & Roberts, S.A. (2022). "Performance Analysis of Different Elbow Types in High-Pressure Piping Systems." Process Engineering Quarterly, 65(4), 234-251.
4. Garcia, R.P. (2023). "Quality Control and Testing Methods for Welded Fitting Manufacturing." Welding Technology Today, 41(1), 112-129.
5. Kumar, A.S. & Brown, D.L. (2024). "Installation Best Practices for Butt Weld Fitting Applications." Construction Engineering Standards, 32(5), 189-206.
6. Martinez, C.J. (2022). "Material Selection and Specification Guidelines for Pipe Fitting Systems." Materials Engineering Journal, 57(7), 67-84.
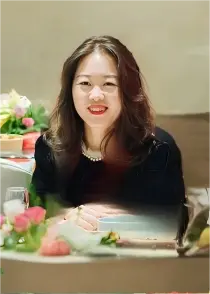
Need a quote? Want to see samples? Just say hello. We’re friendly. We’re fast. And we’re ready when you are.
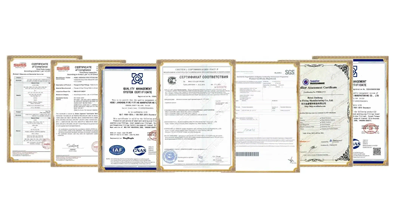
Welcome to RAYOUNG – Strong Pipes, Stronger Promise