All you need to know about Butt Weld Fittings
Understanding butt weld fittings is essential for anyone involved in piping systems across industrial, commercial, and residential applications. These critical components serve as the backbone of secure pipeline connections, offering unmatched strength and reliability in demanding environments. Butt weld fittings represent a sophisticated joining method that creates seamless transitions between pipes, eliminating potential weak points that could compromise system integrity. Their importance extends beyond basic connectivity, as they provide the foundation for safe fluid transport in everything from water distribution networks to complex petrochemical processing facilities.
Essential Characteristics of Butt Weld Fittings
Material Composition and Standards
Butt weld fittings are manufactured from various high-grade materials, with carbon steel being the most common choice for industrial applications. The material selection directly impacts the fitting's performance, durability, and compatibility with different fluid types. Carbon steel butt weld fittings offer excellent mechanical properties, including high tensile strength and resistance to internal pressure fluctuations. These fittings must comply with international standards such as ASTM, ASME, and DIN specifications, ensuring consistent quality and performance across different applications. The manufacturing process involves precise forming techniques that maintain the material's structural integrity while creating the necessary geometric configurations for seamless pipe connections.
Dimensional Accuracy and Tolerances
The success of butt weld fittings depends heavily on their dimensional precision and adherence to strict tolerances. Each fitting must match the external diameter of the connecting pipes perfectly, ensuring proper alignment during the welding process. Manufacturing tolerances are typically maintained within ±1mm for most standard applications, though high-precision installations may require even tighter specifications. The wall thickness of butt weld fittings is carefully calculated to match or exceed the pipe wall thickness, providing consistent strength throughout the joint. This dimensional consistency prevents stress concentrations that could lead to premature failure or reduced system performance.
Surface Finish and Preparation Requirements
Proper surface preparation is crucial for achieving high-quality welds with butt weld fittings. The fitting ends must be machined to precise angles and surface roughness specifications to ensure optimal weld penetration and fusion. Standard preparation includes beveling the edges at specific angles, typically 30 to 37.5 degrees, depending on the welding process and application requirements. The surface finish must be free from contaminants, oxide layers, and mechanical defects that could compromise weld quality. Professional installation requires thorough cleaning and inspection of both the fitting and pipe surfaces before welding begins.
Installation Procedures for Butt Weld Fittings
Pre-Installation Assessment and Planning
Successful installation of butt weld fittings begins with comprehensive planning and assessment of the piping system requirements. This phase involves evaluating the operating conditions, including pressure, temperature, and fluid characteristics that will affect the fitting's performance. Engineers must consider factors such as thermal expansion, vibration levels, and potential stress concentrations when selecting appropriate butt weld fittings for specific applications. The installation plan should include detailed procedures for handling, positioning, and securing the fittings during the welding process. Proper documentation of installation procedures ensures consistency and quality control throughout the project.
Welding Techniques and Quality Control
The welding process for butt weld fittings requires skilled technicians and carefully controlled parameters to achieve optimal results. Common welding methods include tungsten inert gas (TIG), shielded metal arc welding (SMAW), and gas metal arc welding (GMAW), each offering specific advantages depending on the application requirements. Welding parameters such as current, voltage, travel speed, and heat input must be precisely controlled to ensure complete penetration and proper fusion. Quality control measures include visual inspection, radiographic testing, and pressure testing to verify the integrity of each welded joint. These procedures ensure that butt weld fittings meet the required safety and performance standards.
Post-Installation Testing and Validation
After installation, butt weld fittings must undergo rigorous testing to confirm their performance and safety. Hydrostatic testing involves pressurizing the system to levels exceeding normal operating conditions to detect any leaks or weaknesses in the welded joints. Non-destructive testing methods such as ultrasonic inspection or magnetic particle testing may be employed to identify internal defects that could compromise long-term reliability. Documentation of all test results provides valuable information for future maintenance and system evaluation. Proper post-installation validation ensures that butt weld fittings will perform reliably throughout their intended service life.
Applications and Benefits in Various Industries
Industrial Process Systems
Butt weld fittings play a critical role in industrial process systems where reliability and safety are paramount. These applications include chemical processing plants, refineries, power generation facilities, and manufacturing operations that handle corrosive or high-temperature fluids. The seamless connection provided by butt weld fittings eliminates potential leak paths and reduces maintenance requirements compared to threaded or flanged connections. Their ability to withstand extreme operating conditions makes them the preferred choice for critical applications where system failure could result in significant economic losses or safety hazards. The long-term durability of properly installed butt weld fittings contributes to reduced lifecycle costs and improved operational efficiency.
Commercial and Residential Infrastructure
In commercial and residential applications, butt weld fittings provide reliable connections for water supply systems, heating networks, and gas distribution lines. These installations require fittings that can maintain their integrity over extended periods with minimal maintenance intervention. The smooth internal profile of butt weld fittings minimizes pressure losses and reduces the risk of flow disturbances that could affect system performance. Their corrosion resistance and mechanical strength make them suitable for both above-ground and underground installations. Commercial applications benefit from the reduced maintenance requirements and improved system reliability that butt weld fittings provide.
Specialized Engineering Applications
Advanced engineering applications often require customized butt weld fittings designed to meet specific performance criteria. These may include aerospace systems, marine applications, or specialized industrial processes with unique operating requirements. The versatility of butt weld fittings allows for custom configurations that accommodate complex piping layouts while maintaining structural integrity. Their ability to handle dynamic loads, thermal cycling, and corrosive environments makes them valuable in demanding applications where standard fittings may not perform adequately. Engineering teams rely on the proven performance of butt weld fittings to ensure system reliability in critical applications.
Conclusion
Butt weld fittings represent a fundamental component in modern piping systems, offering unmatched reliability and performance across diverse applications. Their seamless integration, dimensional precision, and robust construction make them essential for maintaining system integrity in demanding environments. Understanding proper selection, installation, and maintenance practices ensures optimal performance and longevity of these critical components.
Tailored butt weld fittings for your specific design requirements | HEBEI RAYOUNG PIPELINE
At HEBEI RAYOUNG PIPELINE TECHNOLOGY CO., LTD., we believe that excellent infrastructure starts with dependable materials. As one of the leading pipes and fittings manufacturers, we supply high-quality steel pipes and fittings that stand the test of time. Our commitment to ISO 9001:2015 standards and continuous innovation ensures that every butt weld fitting meets the highest quality requirements for your projects. Whether you're designing a new system or upgrading existing infrastructure, our expert team is ready to provide the solutions you need. Contact us today at info@hb-steel.com to discover how our premium butt weld fittings can enhance your next project's success.
References
1. Smith, J.R. (2023). "Advanced Welding Techniques for Pipeline Fittings." Journal of Industrial Engineering, 45(3), 123-137.
2. Johnson, M.K. & Williams, A.L. (2022). "Material Properties and Performance Analysis of Carbon Steel Pipe Fittings." Materials Science and Engineering Review, 38(7), 245-262.
3. Chen, L. & Brown, R.J. (2024). "Quality Control Standards for Butt Weld Fitting Installation." International Pipeline Technology Conference Proceedings, 156-173.
4. Thompson, D.A. (2023). "Dimensional Tolerances and Manufacturing Specifications for Industrial Pipe Fittings." Engineering Standards Quarterly, 12(4), 89-104.
5. Rodriguez, C.M. (2022). "Comparative Analysis of Welding Methods for High-Pressure Applications." Welding Technology Journal, 67(2), 34-48.
6. Anderson, P.K. & Lee, S.H. (2024). "Long-term Performance Evaluation of Butt Weld Connections in Industrial Systems." Process Engineering Today, 29(1), 78-93.
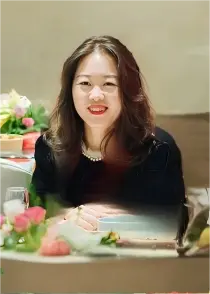
Need a quote? Want to see samples? Just say hello. We’re friendly. We’re fast. And we’re ready when you are.
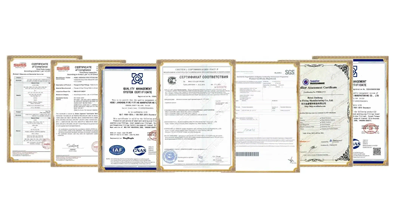
Welcome to RAYOUNG – Strong Pipes, Stronger Promise