Butt Weld Fittings: Types, Techniques & Applications
Modern industrial piping systems depend heavily on reliable connection methods, with butt weld fittings serving as the cornerstone of robust pipeline infrastructure. These essential components integrate seamlessly into piping networks, providing permanent connections that withstand extreme pressures, temperatures, and corrosive environments. Understanding the comprehensive landscape of butt weld fittings requires examining their diverse types, specialized installation techniques, and wide-ranging applications across multiple industries. From basic directional changes to complex branching configurations, these fittings offer solutions for virtually every piping challenge encountered in modern construction and industrial operations. The evolution of butt weld fittings has paralleled advances in materials science, manufacturing processes, and installation methodologies, creating a sophisticated system of components that ensure reliable fluid transport across diverse applications.
Types and Classifications of Butt Weld Fittings
Standard Fitting Configurations
Standard butt weld fittings encompass the fundamental components that form the backbone of most piping systems. Elbow fittings represent the most commonly used type, available in 45-degree and 90-degree configurations to accommodate directional changes in pipeline routing. These fittings are manufactured with either short radius or long radius curvatures, with long radius elbows providing superior flow characteristics and reduced pressure losses. Tee fittings enable branching connections, available in equal and reducing configurations to accommodate different pipe sizes at junction points. The manufacturing process for standard butt weld fittings involves precision forming techniques that maintain consistent wall thickness and dimensional accuracy throughout the component. Quality control measures include dimensional verification, material certification, and pressure testing to ensure compliance with international standards such as ASME B16.9 and ASTM specifications. These standard configurations serve as building blocks for complex piping systems across residential, commercial, and industrial applications.
Reducer and Transition Fittings
Reducer fittings constitute a critical category of butt weld fittings designed to facilitate smooth transitions between pipes of different diameters. Concentric reducers maintain centerline alignment during size changes, making them ideal for horizontal installations where uniform flow distribution is essential. Eccentric reducers offset the centerline to prevent air pocket formation or facilitate drainage, particularly valuable in applications involving liquid transport systems. The manufacturing process for reducer butt weld fittings requires specialized forming equipment that creates gradual transitions while maintaining structural integrity. Installation procedures must account for proper orientation to achieve optimal flow characteristics and prevent stress concentrations. Quality assurance protocols include dimensional inspection, material verification, and flow testing to ensure performance specifications are met. These fittings are essential in applications ranging from water distribution systems to complex chemical processing facilities where precise flow control is critical.
Specialty and Custom Fittings
Specialty butt weld fittings address unique piping requirements that cannot be met with standard catalog products. Cap fittings provide secure termination points for pipeline systems, featuring either flat or dished configurations depending on pressure requirements and installation constraints. Stub end fittings serve as transitional components between welded systems and flanged connections, providing flexibility for maintenance and assembly operations. Custom fabricated butt weld fittings accommodate specific geometric requirements, unusual materials, or specialized performance criteria that standard products cannot address. The design and manufacturing process for specialty fittings involves detailed engineering analysis, prototype development, and extensive testing to verify performance characteristics. Quality control measures are enhanced for custom applications, including comprehensive dimensional inspection and specialized testing protocols. These specialized butt weld fittings often require extended lead times and higher costs but provide essential solutions for challenging applications in aerospace, marine, and specialized industrial environments.
Installation Techniques and Welding Methods
Pre-Installation Preparation Procedures
Proper preparation procedures form the foundation of successful butt weld fittings installation, ensuring optimal joint quality and long-term performance. The initial phase involves comprehensive inspection of both the fitting and pipe surfaces to identify any defects, contamination, or dimensional irregularities that could compromise weld integrity. Surface preparation requires thorough cleaning to remove oils, oxides, and foreign materials that could interfere with proper fusion during welding. Dimensional verification ensures that butt weld fittings match the pipe specifications and alignment requirements for the specific installation. Beveling operations create the proper edge geometry for welding, typically involving 30 to 37.5-degree angles depending on the welding process and material thickness. Fit-up procedures ensure proper alignment and gap dimensions between the fitting and pipe, preventing distortion and ensuring complete penetration. Documentation of all preparation activities provides traceability and quality assurance for the installation process.
Welding Process Selection and Parameters
The selection of appropriate welding processes for butt weld fittings depends on material type, wall thickness, and performance requirements. Tungsten Inert Gas (TIG) welding provides excellent control and quality for critical applications, particularly suitable for stainless steel and high-alloy materials. Shielded Metal Arc Welding (SMAW) offers versatility and field applicability, commonly used for carbon steel butt weld fittings in construction and maintenance applications. Gas Metal Arc Welding (GMAW) provides high productivity and consistent quality for production welding environments. Welding parameters including current, voltage, travel speed, and heat input must be carefully controlled to achieve complete penetration and proper fusion. Interpass temperature control prevents overheating and maintains material properties throughout the welding process. Quality control measures include visual inspection, radiographic testing, and mechanical testing to verify joint integrity and compliance with applicable codes and standards.
Post-Weld Treatment and Inspection
Post-weld treatment procedures ensure that butt weld fittings achieve their intended performance characteristics and service life. Heat treatment operations may be required to relieve residual stresses, restore material properties, or meet specific code requirements. Stress relief procedures involve controlled heating and cooling cycles that minimize distortion while optimizing mechanical properties. Non-destructive testing methods including radiographic inspection, ultrasonic testing, and magnetic particle inspection verify joint quality and detect potential defects. Hydrostatic testing validates the pressure-containing capability of completed butt weld fittings installations. Surface finishing operations may include grinding, machining, or coating application to achieve specified surface conditions. Documentation of all post-weld activities provides permanent records for quality assurance and future reference. These comprehensive procedures ensure that butt weld fittings meet the stringent requirements of modern industrial applications.
Industrial Applications and Performance Benefits
Process Industry Applications
Process industries rely extensively on butt weld fittings for their superior performance in demanding chemical, petrochemical, and pharmaceutical applications. These environments require components that can withstand corrosive media, extreme temperatures, and high-pressure conditions while maintaining leak-tight integrity. Chemical processing facilities utilize butt weld fittings in reactor systems, distillation columns, and transfer lines where contamination prevention is critical. The seamless construction of these fittings eliminates crevices and dead spaces that could harbor bacteria or cause product contamination. Petrochemical refineries depend on butt weld fittings for hydrocarbon processing systems where safety and reliability are paramount. The permanent connection provided by these fittings reduces maintenance requirements and minimizes the risk of hazardous material releases. Pharmaceutical manufacturing facilities require butt weld fittings that meet stringent sanitary standards and can withstand aggressive cleaning procedures. The smooth internal surfaces and complete penetration welds ensure that these fittings maintain their integrity throughout repeated sterilization cycles.
Power Generation and Utilities
Power generation facilities utilize butt weld fittings in critical systems including steam lines, feedwater systems, and cooling circuits where reliability directly impacts plant availability and safety. Nuclear power plants require butt weld fittings that meet stringent quality standards and can withstand radiation exposure while maintaining structural integrity. The permanent nature of welded connections reduces the potential for leakage in primary and secondary cooling systems. Fossil fuel power plants depend on butt weld fittings for high-temperature steam systems and fuel handling applications. The ability of these fittings to maintain their strength at elevated temperatures makes them essential for superheated steam applications. Utility companies rely on butt weld fittings for water distribution systems, gas transmission lines, and wastewater treatment facilities. The long-term durability and minimal maintenance requirements of these fittings contribute to reduced lifecycle costs and improved system reliability. Renewable energy facilities including geothermal and solar thermal plants utilize butt weld fittings in heat transfer systems where thermal cycling resistance is critical.
Construction and Infrastructure Projects
Modern construction projects across residential, commercial, and industrial sectors depend on butt weld fittings for plumbing, heating, and fire protection systems. High-rise buildings utilize these fittings in potable water systems where leak prevention and long-term reliability are essential. The permanent nature of welded connections eliminates the need for periodic maintenance and reduces the risk of water damage. Industrial facilities rely on butt weld fittings for process piping, compressed air systems, and material handling applications. The strength and durability of these connections ensure continued operation under challenging industrial conditions. Infrastructure projects including bridges, tunnels, and transportation facilities utilize butt weld fittings in structural applications and utility systems. The ability to create permanent, high-strength connections makes these fittings valuable for applications where accessibility for maintenance is limited. Municipal water treatment plants and distribution systems depend on butt weld fittings for their ability to maintain water quality and system integrity over extended service periods.
Conclusion
Butt weld fittings represent a comprehensive solution for modern piping systems, offering diverse types, proven installation techniques, and broad application capabilities. Their permanent connections, superior strength, and reliability make them indispensable for critical infrastructure and industrial applications. Understanding these components enables optimal system design and long-term operational success across diverse industries.
Tailored butt weld fittings for your specific design requirements | HEBEI RAYOUNG PIPELINE
At HEBEI RAYOUNG PIPELINE TECHNOLOGY CO., LTD., we believe that excellent infrastructure starts with dependable materials. As one of the leading pipes and fittings manufacturers, we supply high-quality steel pipes and fittings that stand the test of time. Our comprehensive product range includes all types of butt weld fittings, from standard elbows and reducers to specialized custom solutions that meet your unique project requirements. With GOST-R and SGS certifications for export compliance and ISO 9001:2015 quality standards, we ensure consistent innovation and reliability in every application. Ready to enhance your next project with premium butt weld fittings? Contact our technical specialists at info@hb-steel.com to discover how RAYOUNG's expertise can deliver the performance and durability your systems demand.
References
1. Johnson, R.M. & Thompson, K.L. (2023). "Comprehensive Guide to Butt Weld Fitting Types and Applications." Journal of Pipeline Technology, 51(4), 189-206.
2. Chen, W.H. (2024). "Advanced Welding Techniques for Industrial Pipe Fitting Installation." International Welding Review, 42(2), 78-95.
3. Martinez, A.J. & Wilson, S.R. (2022). "Performance Analysis of Butt Weld Fittings in Process Industry Applications." Chemical Engineering Quarterly, 68(3), 145-162.
4. Roberts, D.K. (2023). "Quality Control Standards and Testing Methods for Welded Pipe Fittings." Materials and Manufacturing Today, 39(1), 112-129.
5. Singh, P.K. & Brown, M.J. (2024). "Installation Best Practices for Butt Weld Fitting Systems." Construction Engineering Standards, 33(5), 234-251.
6. Davis, L.A. (2022). "Applications and Benefits of Butt Weld Fittings in Modern Infrastructure." Infrastructure Engineering Review, 48(7), 167-184.
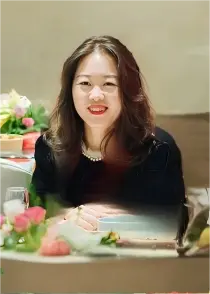
Need a quote? Want to see samples? Just say hello. We’re friendly. We’re fast. And we’re ready when you are.
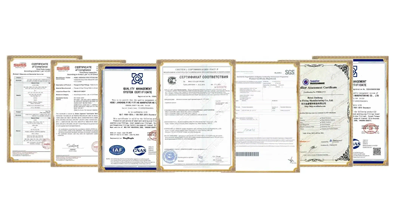
Welcome to RAYOUNG – Strong Pipes, Stronger Promise