Alloy Steel Flanges vs. Stainless Steel Flanges: Which Is Better for Your Project?
Selecting the right material for industrial flanges is a critical decision that impacts project performance, longevity, and cost-efficiency. Both alloy steel and stainless steel flanges offer unique advantages for different applications, making the choice dependent on specific operating conditions and project requirements. Industrial flanges made from these materials serve in demanding environments ranging from high-temperature steam lines to corrosive chemical processing systems. This comprehensive comparison examines the key differences between alloy steel and stainless steel industrial flanges, helping engineers and project managers make informed material selection decisions for their piping systems.
Material Properties and Performance Characteristics
Understanding the fundamental differences between these materials is essential for proper flange selection.
Strength and Temperature Resistance
Alloy steel industrial flanges, particularly those containing chromium and molybdenum (Cr-Mo), excel in high-temperature and high-pressure applications. Grades like ASTM A182 F11, F22, and F91 maintain their structural integrity at elevated temperatures up to 650°C, making them ideal for power plants and refinery services. The added alloying elements enhance creep resistance and tensile strength under thermal cycling conditions. Stainless steel industrial flanges, while offering good strength, typically have lower maximum service temperatures than their alloy steel counterparts, though certain austenitic grades like 316H and 347H are specifically designed for elevated temperature service.
Corrosion Resistance Capabilities
Stainless steel industrial flanges naturally resist corrosion due to their chromium content (minimum 10.5%), which forms a passive oxide layer on the surface. Austenitic grades like 304 and 316L offer excellent resistance to a wide range of chemicals, making them suitable for food processing, pharmaceutical, and marine applications. Alloy steel flanges require additional protection in corrosive environments, often through coatings or cathodic protection systems. However, certain alloy steel compositions provide better resistance to specific corrosive agents like sulfur compounds found in oil and gas applications, demonstrating that material performance depends heavily on the exact service environment.
Toughness and Impact Resistance
Industrial flanges made from low-temperature grade stainless steels (such as 304L or 316L) maintain excellent toughness down to cryogenic temperatures, making them preferred for LNG and cryogenic applications. Alloy steels generally have better impact resistance at moderate temperatures but require special low-temperature grades (like A350 LF2) for sub-zero services. The duplex stainless steel family (e.g., 2205) combines good toughness with superior stress corrosion cracking resistance, bridging the gap between conventional stainless and alloy steel industrial flanges in certain demanding applications.
Cost Considerations and Lifecycle Analysis
The economic factors of flange selection extend beyond initial material costs.
Initial Purchase Price Comparison
Stainless steel industrial flanges typically command a higher initial price compared to alloy steel counterparts, with the cost difference varying by specific grade and market conditions. Austenitic stainless steel flanges (304, 316) generally cost 2-3 times more than comparable carbon or low-alloy steel flanges, while premium grades like super duplex or nickel alloys can be significantly more expensive. Alloy steel industrial flanges offer a cost advantage in applications where their specific properties are sufficient, particularly in high-temperature services where stainless steels might require thicker sections or additional supports to compensate for lower strength at elevated temperatures.
Installation and Maintenance Costs
The total cost of ownership for industrial flanges includes installation, maintenance, and potential replacement expenses. Stainless steel's corrosion resistance often reduces maintenance needs in aggressive environments, potentially offsetting higher initial costs over time. Alloy steel flanges may require more frequent inspection, protective coatings, or cathodic protection in corrosive services. However, alloy steel's generally better machinability can reduce fabrication costs for custom flange configurations. The weight difference between materials also affects installation costs, with stainless steel's higher density potentially requiring more substantial support structures in large-diameter piping systems.
Expected Service Life and Replacement Cycles
When properly specified for their operating environment, both alloy steel and stainless steel industrial flanges can provide decades of reliable service. Stainless steel typically offers longer lifespan in corrosive or marine environments without additional protection. Alloy steel performs exceptionally well in high-temperature, high-pressure hydrocarbon services where creep resistance is critical. Lifecycle cost analysis should consider not just flange replacement costs but also the potential consequences of failure, including production losses and safety implications, which often favor investing in the most suitable material regardless of initial price differences.
Industry-Specific Applications and Selection Guidelines
Optimal flange material selection depends heavily on the intended application.
Oil and Gas Industry Requirements
In upstream oil and gas applications, alloy steel industrial flanges (particularly Cr-Mo grades) dominate high-pressure, high-temperature wellhead and production piping systems due to their strength and resistance to hydrogen attack. Stainless steel finds more use in downstream processing where corrosion from acids and other chemicals becomes a concern. Offshore platforms often employ duplex stainless steel flanges for their combination of strength and chloride resistance. The choice between materials in this industry frequently comes down to the specific service fluid composition, temperature, and pressure conditions.
Chemical and Petrochemical Processing
Stainless steel industrial flanges are prevalent in chemical plants handling corrosive media, with grade selection based on the specific chemicals involved. 316/L stainless steel resists a wide range of acids and chlorides, while more aggressive environments may require super austenitic or duplex grades. Alloy steels see use in utility and non-corrosive process streams where their mechanical properties provide advantages. Many chemical plants implement a mix of both materials, selecting stainless steel for corrosive services and alloy steel for high-energy systems like steam distribution.
Power Generation Applications
Power plants utilize both material types extensively, with selection based on temperature and pressure requirements. Alloy steel industrial flanges (especially grades F11, F22, and F91) are standard for high-pressure steam lines and boiler components where creep resistance is paramount. Stainless steel finds application in condenser cooling water systems and auxiliary processes where corrosion resistance outweighs the need for extreme temperature capability. Modern combined-cycle plants often feature a strategic combination of both materials, optimizing performance while controlling costs across different system sections.
Conclusion
Choosing between alloy steel and stainless steel industrial flanges requires careful evaluation of operating conditions, performance requirements, and lifecycle costs. Alloy steel excels in high-temperature, high-pressure applications, while stainless steel provides superior corrosion resistance. The optimal selection depends on specific project parameters, with many industrial installations benefitting from a strategic combination of both materials throughout different system sections.
HEBEI RAYOUNG PIPELINE: Your Trusted Industrial Flange Manufacturer
HEBEI RAYOUNG PIPELINE TECHNOLOGY CO., LTD manufactures high-quality industrial flanges in both alloy steel and stainless steel to meet diverse project requirements. Our ISO 9001:2015 certified facility produces flanges that comply with international standards including ASME, ANSI, DIN, and GOST specifications. Whether you need the high-temperature performance of alloy steel or the corrosion resistance of stainless steel, we offer solutions tailored to your specific operating conditions.
Contact our technical team today at info@hb-steel.com to discuss your project needs and receive expert guidance on flange material selection for optimal performance and value.
References
1. ASME B16.5 - Pipe Flanges and Flanged Fittings
2. ASTM A182/A182M - Standard Specification for Forged or Rolled Alloy and Stainless Steel Pipe Flanges
3. NACE MR0175/ISO 15156 - Materials for use in H2S-containing environments
4. ASME Boiler and Pressure Vessel Code, Section II - Materials
5. API 6A - Specification for Wellhead and Christmas Tree Equipment
6. EN 1092-1 - Flanges and their joints - Circular flanges for pipes, valves, fittings and accessories
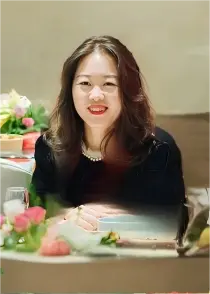
Need a quote? Want to see samples? Just say hello. We’re friendly. We’re fast. And we’re ready when you are.
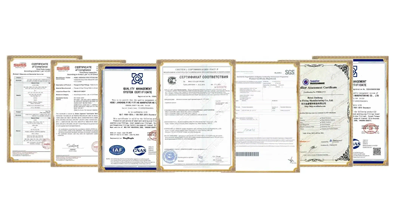
Welcome to RAYOUNG – Strong Pipes, Stronger Promise