The Benefits of Using Reducing Flanges in Industrial Processes
Reducing flanges play a crucial role in modern industrial piping systems by enabling efficient transitions between pipes of different diameters. These specialized industrial flanges provide numerous advantages over alternative reduction methods, offering improved flow characteristics, space savings, and simplified installation. As essential components in chemical plants, oil refineries, water treatment facilities, and other industrial settings, reducing flanges help optimize piping system performance while maintaining structural integrity. This article explores the key benefits of incorporating reducing industrial flanges in process piping, examining their operational advantages, cost efficiencies, and application-specific benefits that make them preferred solutions for diameter transitions in demanding industrial environments.
Operational Advantages of Reducing Flanges
Smooth Flow Transition and Reduced Turbulence
Unlike concentric reducers that create abrupt diameter changes, reducing industrial flanges provide a more gradual transition between pipe sizes. This design minimizes flow turbulence and pressure drops, particularly important in systems handling viscous fluids or where laminar flow is desired. The engineered geometry of quality reducing flanges maintains efficient fluid dynamics while preventing the vortex formation common in poorly designed transitions. In pump discharge lines and other critical flow applications, properly specified reducing industrial flanges can significantly improve system efficiency and reduce energy consumption compared to alternative reduction methods.
Space Optimization in Compact Installations
Reducing industrial flanges offer substantial space savings compared to using separate reducer fittings with standard flanges. This consolidated design is particularly valuable in crowded industrial plants where piping real estate is limited. By eliminating the need for additional pipe spools and flange pairs, reducing flanges simplify piping layouts in equipment-dense areas like compressor stations, heat exchanger banks, and vessel manifolds. Their compact footprint also facilitates maintenance access in tight spaces, allowing easier disassembly and reassembly during equipment servicing or system modifications.
Enhanced Structural Integrity at Transition Points
The monolithic construction of reducing industrial flanges provides superior strength at diameter transition points compared to reducer-flange combinations. This integrated design eliminates potential weak points that can develop at welded joints between separate components. High-quality reducing flanges distribute stress more evenly across the transition zone, making them particularly suitable for systems experiencing thermal cycling, vibration, or pressure fluctuations. Their robust construction also better withstands the mechanical loads encountered during bolt tightening and system pressurization, reducing the risk of leaks at critical transition points.
Cost and Installation Benefits
Implementing reducing flanges generates tangible economic advantages throughout the project lifecycle.
Material and Labor Cost Savings
Reducing industrial flanges reduce overall project costs by minimizing the number of required components. A single reducing flange replaces the need for a separate reducer fitting plus two standard flanges, resulting in significant material savings, especially in large-diameter piping systems. The simplified design also cuts welding and installation labor costs, as it eliminates two potential weld joints (reducer-to-pipe connections) from each transition point. These savings multiply across large industrial projects with numerous diameter changes, making reducing flanges a cost-effective choice for budget-conscious installations without compromising quality or performance.
Simplified Inventory Management
Standardizing on reducing industrial flanges simplifies piping component inventories by reducing the variety of parts needed for diameter transitions. Maintenance teams benefit from having fewer spare parts to stock, and procurement departments face less complexity in material ordering. This streamlined approach reduces the risk of installation errors caused by mismatched components and minimizes downtime during repairs or modifications. Many industrial facilities find that adopting reducing flanges as their standard for diameter transitions improves overall materials management efficiency while maintaining system flexibility.
Reduced Maintenance Requirements
The robust, leak-resistant design of quality reducing industrial flanges translates to lower long-term maintenance costs. Their integrated construction eliminates potential failure points present in reducer-flange combinations, reducing the frequency of inspections and repairs. Properly installed reducing flanges maintain their integrity through numerous pressure and thermal cycles, minimizing unplanned shutdowns for gasket replacements or joint repairs. In corrosive services, high-grade reducing flanges with appropriate material specifications demonstrate excellent resistance to degradation, further extending service intervals and reducing lifecycle maintenance expenses.
Application-Specific Benefits
Reducing flanges provide targeted advantages in various industrial settings.
Chemical and Petrochemical Processing
In chemical plants, reducing industrial flanges offer exceptional compatibility with aggressive media when manufactured in corrosion-resistant alloys. Their smooth transitions prevent product buildup in processes handling polymers, slurries, or crystallizing compounds. The elimination of crevices between separate components reduces areas where corrosive agents can concentrate, enhancing overall system reliability. Many chemical processors specify reducing flanges for critical transitions in reactor feed lines, distillation columns, and heat exchanger connections where leak prevention is paramount.
Oil and Gas Pipeline Systems
The oil and gas industry benefits from reducing industrial flanges in manifold systems, compressor stations, and pipeline tie-ins. Their space-saving design is particularly valuable on offshore platforms where deck space is limited. High-pressure reducing flanges with proper metallurgy withstand the demanding conditions of hydrocarbon service while providing reliable transitions between different line sizes. The reduced number of potential leak points also enhances safety in flammable service, making them preferred solutions for critical diameter changes in upstream and midstream applications.
Water Treatment and Distribution
Municipal water systems utilize reducing industrial flanges at pump stations, treatment plant process lines, and distribution network transitions. Their smooth bore minimizes head loss in high-flow applications, improving system efficiency. The corrosion-resistant varieties (including cement-lined and epoxy-coated options) provide long service life in both potable water and wastewater applications. Many water utilities appreciate how reducing flanges simplify the connection of different pipe materials (such as transitioning between ductile iron and steel lines) while maintaining system integrity and leak resistance.
Conclusion
Reducing flanges deliver comprehensive benefits for industrial piping systems, combining operational efficiency, cost savings, and application-specific advantages. Their superior flow characteristics, space optimization, and structural integrity make them ideal solutions for diameter transitions across various industries. By reducing component counts and maintenance requirements while improving system reliability, quality reducing industrial flanges represent a smart investment for modern process plants and infrastructure projects.
RAYOUNG PIPELINE:Your Trusted Reducing industrial Flange Manufacturer
HEBEI RAYOUNG PIPELINE TECHNOLOGY CO., LTD specializes in manufacturing high-quality reducing industrial flanges that meet international standards including ANSI, ASME, and DIN specifications. Our ISO 9001:2015 certified production facility offers reducing flanges in various materials, sizes, and pressure ratings to suit diverse industrial applications. With GOST-R and SGS certifications ensuring quality compliance, we provide reliable solutions for oil & gas, chemical processing, water treatment, and other demanding industries.
Contact our technical experts today at info@hb-steel.com to discuss your reducing flange requirements and discover how our products can optimize your piping systems.
References
1. ASME B16.5 - Pipe Flanges and Flanged Fittings
2. ASME B16.47 - Large Diameter Steel Flanges
3. API 6A - Specification for Wellhead and Christmas Tree Equipment
4. EN 1092-1 - Flanges and their joints
5. MSS SP-44 - Steel Pipeline Flanges
6. ASME B31.3 - Process Piping
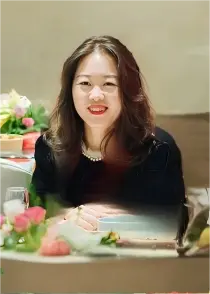
Need a quote? Want to see samples? Just say hello. We’re friendly. We’re fast. And we’re ready when you are.
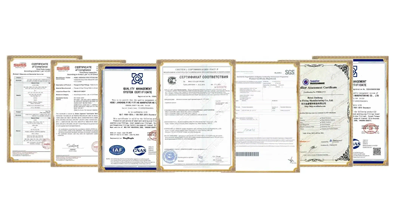
Welcome to RAYOUNG – Strong Pipes, Stronger Promise