What Flanges are Used in the Oil and Gas Industry?
Industrial flanges play a critical role in oil and gas operations, providing secure, leak-proof connections for high-pressure piping systems that transport hydrocarbons and process fluids. The extreme operating conditions in upstream, midstream, and downstream operations demand specialized industrial flanges that can withstand high pressures, corrosive environments, and temperature fluctuations. This article examines the key types of industrial flanges used across the oil and gas sector, their material specifications, and application-specific requirements that ensure safe and efficient operations in one of the world's most demanding industrial environments.
Primary Flange Types in Oil and Gas Operations
The oil and gas industry utilizes several specialized industrial flanges designed for specific operational requirements.
Weld Neck Flanges for High-Pressure Systems
Weld neck industrial flanges are the most common type used in critical oil and gas applications due to their superior strength and leak resistance. These flanges feature a long tapered hub that provides reinforcement in high-stress areas, making them ideal for wellhead equipment, production manifolds, and high-pressure transmission lines. The smooth transition from flange thickness to pipe wall minimizes turbulence and erosion at the connection point. In offshore platforms and subsea applications, specially engineered weld neck industrial flanges with enhanced corrosion protection are standard, often incorporating cathodic protection systems and advanced coatings to combat seawater exposure.
Ring-Type Joint (RTJ) Flanges for Critical Services
RTJ industrial flanges incorporate precision-machined grooves that accommodate metal ring gaskets, creating exceptionally reliable seals in high-pressure hydrocarbon service. These flanges are mandatory for wellhead equipment, Christmas trees, and other critical pressure-containing components. The metal-to-metal seal provided by RTJ industrial flanges maintains integrity even under extreme pressure and temperature cycling, preventing dangerous leaks of flammable or toxic substances. Their robust design makes them particularly suitable for sour gas service (H2S-containing environments) where leak prevention is paramount for safety and environmental protection.
Blind Flanges for System Isolation and Testing
Blind industrial flanges serve as removable pipe end closures in oil and gas facilities, allowing for system isolation, maintenance access, and pressure testing. These solid discs are essential components during pipeline hydrotesting and system commissioning procedures. In process plants, blind industrial flanges safely isolate equipment for maintenance while maintaining the integrity of connected systems. Special variants like spectacle blinds provide permanent installation options for systems requiring periodic isolation. The thickness of blind flanges increases with pressure class to withstand substantial internal forces in oil and gas applications.
Material Specifications and Performance Requirements
Oil and gas industrial flanges must meet stringent material standards to ensure reliability in harsh operating conditions.
Carbon and Alloy Steel Flanges
ASTM A105 carbon steel industrial flanges are widely used in general oil and gas services, while ASTM A182 alloy steel grades (F11, F22, F91) are specified for high-temperature applications like refinery process piping and steam systems. These materials offer excellent strength and durability while maintaining cost-effectiveness for large-diameter pipelines. For low-temperature services such as LNG facilities, impact-tested grades like A350 LF2 ensure adequate toughness at sub-zero temperatures. The oil and gas industry often requires supplementary chemical composition controls and enhanced testing for industrial flanges used in sour service (NACE MR0175/ISO 15156 compliance).
Corrosion-Resistant Alloys
In corrosive environments like offshore platforms or sour gas fields, stainless steel and nickel alloy industrial flanges provide essential protection. Austenitic stainless steels (316/L, 317L) resist chloride attack in marine environments, while duplex and super duplex stainless steels offer superior strength and corrosion resistance. For extremely aggressive conditions, nickel alloys like Inconel 625 or Hastelloy C276 may be specified. These premium materials command higher prices but deliver extended service life in critical applications, often proving more cost-effective than carbon steel with repeated maintenance or replacement.
Special Coatings and Treatments
Industrial flanges in oil and gas service frequently receive specialized surface treatments to enhance performance. Internal epoxy coatings protect against corrosive fluids, while external fusion-bonded epoxy (FBE) or three-layer polyolefin coatings prevent soil corrosion in buried pipelines. Offshore applications may utilize sacrificial anode systems or impressed current cathodic protection. For high-wear applications like sand slurry lines, industrial flanges may feature tungsten carbide coatings or ceramic linings to resist erosive damage from particulate matter in the flow stream.
Application-Specific Flange Solutions
Different segments of the oil and gas industry require tailored industrial flange solutions.
Upstream Exploration and Production
Wellhead equipment utilizes specialized industrial flanges designed to API 6A specifications, with pressure ratings up to 20,000 psi for some applications. These flanges incorporate ring-type joints and are manufactured from materials resistant to sour service conditions. Production manifolds employ compact flange designs to minimize space requirements on crowded offshore platforms. Subsea industrial flanges feature enhanced corrosion protection and often incorporate hub-and-clamp connections for easier installation in underwater environments.
Midstream Transportation
Pipeline industrial flanges for transmission systems balance strength requirements with installation practicality. Large-diameter flanges (ASME B16.47 Series A/B) connect major pipeline segments, while compact flange designs simplify installation in compressor stations and meter runs. Pipeline operators increasingly prefer welded connections for main lines but retain industrial flanges at strategic locations for maintenance access and system modifications. Special insulation kits may be installed on flanges in electrically isolated pipeline sections to maintain cathodic protection systems.
Refining and Petrochemical Processing
Refinery industrial flanges must withstand extreme temperatures and aggressive chemicals. High-alloy materials resist sulfidation and high-temperature hydrogen attack in crude and vacuum distillation units. Reactor feed systems utilize industrial flanges with specialized gasketing to prevent leaks of volatile organic compounds. The petrochemical sector often specifies stainless steel or nickel alloy flanges for processes involving acids, caustics, or other corrosive media. Heat exchanger connections employ industrial flanges designed for frequent disassembly during maintenance and cleaning cycles.
Conclusion
The oil and gas industry relies on carefully engineered industrial flanges that meet exacting standards for safety, reliability, and performance. From high-pressure wellhead equipment to corrosion-resistant refinery piping, proper flange selection and specification are critical for maintaining operational integrity. Understanding the various types, materials, and application requirements ensures optimal flange performance throughout the hydrocarbon value chain.
RAYOUNG PIPELINE:Your Trusted Flange Manufacturer
HEBEI RAYOUNG PIPELINE TECHNOLOGY CO., LTD manufactures high-quality industrial flanges specifically designed for oil and gas applications. Our ISO 9001:2015 certified facility produces flanges that comply with API, ASME, ANSI, and other international standards. Whether you need standard carbon steel flanges or specialized corrosion-resistant alloys, we provide solutions tailored to your operational requirements and environmental conditions.
Contact our specialists today at info@hb-steel.com to discuss your project needs and receive expert recommendations for optimal flange selection and performance.
References
1. API 6A - Specification for Wellhead and Christmas Tree Equipment
2. ASME B16.5 - Pipe Flanges and Flanged Fittings
3. NACE MR0175/ISO 15156 - Materials for use in H2S-containing environments
4. ASME B16.47 - Large Diameter Steel Flanges
5. API 17D - Subsea Wellhead and Christmas Tree Equipment
6. ASME B31.3 - Process Piping
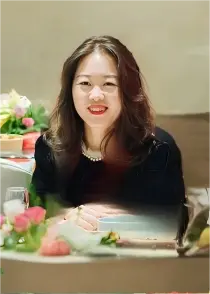
Need a quote? Want to see samples? Just say hello. We’re friendly. We’re fast. And we’re ready when you are.
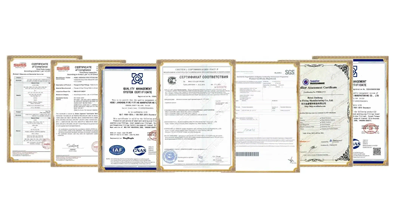
Welcome to RAYOUNG – Strong Pipes, Stronger Promise