Flange Basics: Functions, Designs, and Other Considerations
Pipe flanges are essential components in industrial piping systems, providing secure, leak-proof connections between pipes, valves, pumps, and other equipment. They enable easy assembly, disassembly, and maintenance while accommodating different pressure ratings, temperatures, and fluid types. Understanding flange functions, designs, and selection criteria ensures optimal performance in applications ranging from water distribution to high-pressure oil and gas pipelines. This guide explores the fundamental aspects of pipe flanges, including their primary roles, common designs, and key factors influencing their selection and installation.
Core Functions of Pipe Flanges
Pipe flanges serve multiple critical purposes in piping systems, ensuring structural integrity, flexibility, and safety across various industrial applications.
Creating Secure, Leak-Proof Connections
The primary function of pipe flanges is to join piping sections while maintaining a tight seal under operational pressures. Flanges use gaskets between mating surfaces to prevent leaks, with bolt tension ensuring uniform compression. Different flange faces—such as raised face (RF), flat face (FF), and ring-type joint (RTJ)—are designed for specific sealing requirements. High-pressure systems often employ RTJ flanges with metal gaskets, while RF flanges with non-metallic gaskets suffice for lower pressures. Proper bolt tightening sequences and torque values are crucial to achieving a reliable seal without damaging the flange or gasket.
Facilitating Maintenance and System Modifications
Unlike welded connections, pipe flanges allow for easy disassembly, making them ideal for systems requiring frequent inspections, cleaning, or modifications. This is particularly valuable in industries like chemical processing, where equipment must be regularly serviced or replaced. Slip-on and lap joint flanges simplify alignment during reassembly, reducing downtime during maintenance. Blind flanges act as removable end caps, enabling future system expansions or pressure testing. The modularity provided by flanged connections enhances operational flexibility while minimizing disruption to adjacent piping.
Accommodating Thermal Expansion and Vibration
Piping systems experience thermal cycling and mechanical vibrations that can stress rigid connections. Pipe flanges, when properly designed, absorb some of these dynamic forces, reducing the risk of fatigue failure. Expansion joint flanges incorporate flexible elements to handle significant thermal movement in high-temperature applications like steam lines. In vibrating systems, such as compressor or pump discharge lines, flanges with resilient gaskets help dampen vibrations that could otherwise lead to bolt loosening or joint failure over time.
Typical Flange Designs and Uses for Them
Selecting the right flange design depends on system pressure, temperature, fluid characteristics, and installation requirements.
Weld Neck Flanges for High-Pressure Systems
Weld neck flanges feature a tapered hub that reinforces the connection, making them suitable for high-pressure and high-temperature applications. The smooth transition from flange to Pipe Flanges minimizes stress concentrations, reducing the risk of failure under cyclic loading. These flanges are commonly used in oil and gas pipelines, power plants, and chemical processing industries. Their extended neck allows for full penetration welding, ensuring maximum strength and facilitating non-destructive testing (NDT) for quality assurance.
Slip-On Flanges for Cost-Effective Solutions
Slip-on flanges are popular in low to medium-pressure systems due to their ease of installation and lower material cost. They slide over the pipe and are secured with fillet welds on both the inner and outer edges. While not as robust as weld neck flanges, they are widely used in water treatment, HVAC, and general industrial applications where extreme conditions are not a concern. Proper alignment during welding is critical to prevent misalignment and ensure a leak-free joint.
Threaded Flanges for Non-Welded Connections
Threaded flanges screw onto pipes with matching external threads, eliminating the need for welding. This makes them ideal for explosive environments, small-diameter piping, or situations where welding is impractical. They are commonly found in fuel gas systems, instrumentation lines, and compressed air networks. However, their pressure rating is limited compared to welded flanges, and thread sealants are necessary to prevent leaks.
Important Things to Think About When Choosing and Installing Flanges
Choosing the right flange involves evaluating material compatibility, pressure ratings, and environmental factors.
Material Selection Based on Service Conditions
Pipe flanges are manufactured from carbon steel, stainless steel, alloy steel, and non-metallic materials, each suited for specific environments. Carbon steel flanges (ASTM A105) are cost-effective for general applications, while stainless steel (ASTM A182) resists corrosion in chemical or marine settings. For highly corrosive media, alloy flanges like Hastelloy or titanium may be required. Temperature extremes also influence material choice—low-temperature services often use impact-tested carbon steel, while high-temperature applications may require chrome-moly alloys.
Pressure Class and Dimensional Standards
Flanges are classified by pressure ratings (e.g., ANSI 150, 300, 600) that dictate their maximum allowable working pressure (MAWP). Matching the flange class to system requirements prevents over- or under-specification. Dimensional standards (ASME B16.5, EN 1092-1) ensure compatibility between flanges from different manufacturers. Proper bolt selection—grade, length, and lubrication—is equally critical to maintaining joint integrity under operational stresses.
Gasket and Bolting Considerations
The gasket material must be compatible with the fluid, temperature, and pressure. Spiral-wound gaskets with stainless steel windings and graphite filler are common for high-pressure steam, while PTFE gaskets suit corrosive chemicals. Bolt tightening procedures—such as cross-pattern torque application—ensure even gasket compression. Hydraulic tensioning tools may be used in critical applications to achieve precise bolt loads and prevent flange distortion.
Conclusion
Pipe flanges play a vital role in ensuring safe, reliable, and maintainable piping systems across industries. Understanding their functions, designs, and selection criteria helps engineers optimize performance while minimizing leaks and failures. From material compatibility to proper installation techniques, every detail contributes to the long-term integrity of flanged connections.
Trust HEBEI RAYOUNG for High-Quality Pipe Flanges
At HEBEI RAYOUNG PIPELINE TECHNOLOGY CO., LTD, we manufacture precision-engineered pipe flanges that meet global standards, including ASME, ANSI, and DIN specifications. Our ISO 9001:2015 certified production ensures consistent quality, whether you need weld neck, slip-on, threaded, or specialty flanges for demanding applications.
Contact us today at info@hb-steel.com to discuss your project requirements—let’s build piping systems that stand the test of time!
References
1. ASME B16.5 - Pipe Flanges and Flanged Fittings
2. ASME B16.47 - Large Diameter Steel Flanges
3. API 6A - Specification for Wellhead and Christmas Tree Equipment
4. EN 1092-1 - Flanges and Their Joints
5. MSS SP-44 - Steel Pipeline Flanges
6. ASME Boiler and Pressure Vessel Code, Section VIII - Pressure Vessels
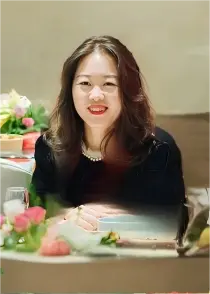
Need a quote? Want to see samples? Just say hello. We’re friendly. We’re fast. And we’re ready when you are.
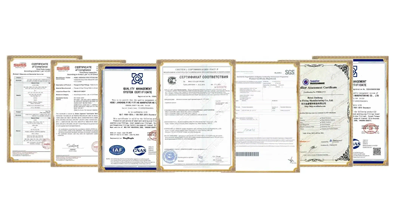
Welcome to RAYOUNG – Strong Pipes, Stronger Promise