Everything You Need to Know About Flanges for Pipes
Pipe flanges are indispensable components in modern piping systems, serving as the critical connection points that join pipes, valves, pumps and other equipment while allowing for maintenance access and system modifications. These circular discs with bolt holes come in various materials, pressure ratings and face configurations to accommodate different industrial requirements. From high-pressure steam lines to chemical processing plants, the proper selection and installation of pipe flanges directly impacts system integrity, safety and longevity. This comprehensive guide covers all essential aspects of pipe flanges, including their fundamental types, material considerations, installation best practices, and industry-specific applications to help engineers and procurement specialists make informed decisions.
Fundamental Types of Pipe Flanges
Understanding the different flange types is crucial for selecting the appropriate connection method based on pressure requirements, installation constraints and maintenance needs.
Weld Neck Flanges for Critical Applications
Weld neck flanges (WN) feature a long tapered hub that provides reinforcement in high-stress applications, making them the preferred choice for extreme pressure and temperature conditions in oil/gas and power generation industries. The smooth transition from flange thickness to pipe wall significantly reduces stress concentration points compared to other flange types. These pipe flanges require butt welding to the pipe, creating a robust connection that allows for radiographic inspection of the weld joint - a critical requirement in regulated industries. The extended neck also helps minimize turbulence and erosion at the connection point, particularly important for high-velocity fluid systems.
Slip-On Flanges for Cost-Effective Solutions
Slip-on pipe flanges (SO) offer installation advantages with their lower initial cost and simpler welding requirements compared to weld neck varieties. The flange slides over the pipe and requires only two fillet welds (inside and outside), making them popular for low-to-medium pressure applications like water distribution and HVAC systems. While not suitable for severe cyclic loading conditions, their ease of alignment proves beneficial during piping modifications or expansions. Many engineers specify slip-on flanges for systems operating below 300 psi where the reduced material and labor costs provide significant savings without compromising safety in static applications.
Blind Flanges for System Isolation
Blind pipe flanges (BL) serve as removable closures in piping systems, allowing for future expansion, maintenance access or pressure testing. These solid discs without a center hole can withstand full system pressure when properly bolted, making them essential components during hydrotesting and system commissioning. In process plants, they safely isolate equipment for maintenance while maintaining the integrity of the overall system. Special variants include spectacle blinds (combination of blind and spacer) for permanent installation in systems requiring periodic isolation, demonstrating the versatility of these critical piping components.
Selection of Materials and Their Details
Choosing the right material for pipe flanges involves careful consideration of fluid compatibility, temperature ranges and environmental factors.
Carbon Steel Flanges for General Service
ASTM A105 carbon steel pipe flanges are the most common choice for general service applications involving water, oil and gas in moderate temperature ranges. These flanges offer excellent strength and durability at a reasonable cost, with normal operating temperatures between -29°C to 425°C. For low-temperature services down to -46°C, impact-tested A350 LF2 flanges are specified to prevent brittle fracture. Carbon steel flanges are typically hot-dip galvanized for corrosion protection in outdoor applications, though the zinc coating must be removed from sealing surfaces to ensure proper gasket performance.
Stainless Steel Flanges for Corrosive Environments
ASTM A182 stainless steel pipe flanges (grades 304, 316, 316L) provide superior corrosion resistance for chemical processing, marine and food-grade applications. The chromium content forms a passive oxide layer that naturally resists oxidation, while molybdenum in 316/316L grades enhances resistance to chlorides and acidic media. For highly corrosive environments, super duplex stainless steels (UNS S32750) and nickel alloys like Inconel offer exceptional pitting and stress corrosion cracking resistance. These premium materials command higher prices but deliver extended service life in aggressive media, often proving more cost-effective long-term.
Special Alloys and Coatings
In extreme service conditions, pipe flanges may require specialized alloys like Hastelloy, Monel or titanium to handle particularly aggressive chemicals or high temperatures. Alternatively, carbon steel flanges can be lined with corrosion-resistant materials like PTFE, rubber or glass-reinforced epoxy for specific chemical resistance at lower cost than solid alloy flanges. Recent advancements in metallurgical coatings, including HVOF (High-Velocity Oxygen Fuel) applied tungsten carbide, provide exceptional erosion resistance for abrasive slurry applications while maintaining dimensional accuracy of the flange faces.
Recommended Practices for Installation and Maintenance
Proper installation techniques and ongoing maintenance are essential for ensuring leak-free performance throughout the service life of pipe flanges.
Proper Bolt Tightening Procedures
Achieving uniform bolt load is critical for creating and maintaining a reliable seal in pipe flanges. Industry standards recommend using calibrated torque wrenches and following specific tightening patterns (typically star/cross patterns) to ensure even gasket compression. For critical applications, hydraulic bolt tensioners provide more precise loading and are particularly useful for large diameter flanges. Proper lubrication of bolt threads and washers reduces friction variability that can lead to uneven loading. Many operators now implement digital torque monitoring systems that record installation data for quality assurance and future maintenance reference.
Gasket Selection and Installation
The gasket forms the primary seal between pipe flanges and must be carefully selected based on pressure, temperature, fluid compatibility and flange face type. Common gasket materials include compressed non-asbestos fiber for low-pressure applications, spiral-wound (stainless steel with graphite/filler) for intermediate conditions, and solid metal ring-type joints for high-pressure/temperature services. Proper gasket installation requires clean, undamaged flange faces with appropriate surface finish (typically 125-250 microinches for raised face flanges). Gaskets should never be reused, and alignment must be carefully maintained during assembly to prevent pinching or buckling.
Inspection and Maintenance Protocols
Regular inspection of pipe flanges can identify potential issues before they develop into leaks or failures. Common inspection methods include visual checks for corrosion or bolt loosening, ultrasonic thickness measurements to detect wall thinning, and thermographic surveys to identify hot spots indicating gasket degradation. Maintenance programs should include periodic re-torquing of bolts, especially during system heat-up cycles in thermal applications. For flanges in corrosive services, cathodic protection or protective coatings may be necessary to extend service life. Proper documentation of all flange installations, including bolt torque values and gasket specifications, facilitates future maintenance and troubleshooting.
Conclusion
Pipe flanges are far more than simple connecting pieces - they are engineered components whose proper selection, installation and maintenance directly impact system reliability and safety. Understanding the various types, materials and installation best practices enables engineers to design robust piping systems capable of withstanding operational demands. From material compatibility studies to precision bolt tightening procedures, every detail contributes to the long-term performance of these critical connections in industrial piping networks.
HEBEI RAYOUNG PIPELINE:Your Trusted Partner for Premium Pipe Flanges
HEBEI RAYOUNG PIPELINE TECHNOLOGY CO., LTD specializes in manufacturing high-quality pipe flanges that meet the most demanding industrial requirements. Our ISO 9001:2015 certified facility produces ANSI/ASME, DIN, JIS and GOST compliant flanges in carbon steel, stainless steel and specialty alloys. With GOST-R and SGS certifications ensuring international compliance, we supply reliable flange solutions for oil & gas, chemical processing, power generation and water treatment applications worldwide.
Contact our technical team today at info@hb-steel.com to discuss your project specifications and discover how our flange solutions can enhance your piping system's performance and reliability.
References
1. ASME B16.5 - Pipe Flanges and Flanged Fittings
2. ASME B16.47 - Large Diameter Steel Flanges
3. API 6A - Specification for Wellhead and Christmas Tree Equipment
4. EN 1092-1 - Flanges and their joints - Circular flanges for pipes, valves, fittings and accessories
5. MSS SP-44 - Steel Pipeline Flanges
6. ASME Boiler and Pressure Vessel Code, Section VIII - Rules for Construction of Pressure Vessels
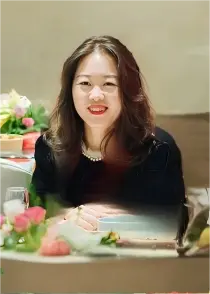
Need a quote? Want to see samples? Just say hello. We’re friendly. We’re fast. And we’re ready when you are.
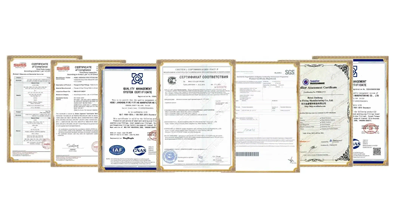
Welcome to RAYOUNG – Strong Pipes, Stronger Promise