Preventing Corrosion in Industrial Pipe and Fittings
Corrosion poses one of the most persistent threats to the longevity and reliability of industrial pipe components across various sectors. From chemical processing plants to municipal water systems, the gradual degradation of metal pipes and fittings can lead to catastrophic failures, environmental hazards, and costly downtime. Implementing effective corrosion prevention strategies is not just about maintenance—it's about selecting the right materials, applying advanced protective technologies, and establishing rigorous monitoring protocols. This comprehensive guide explores three fundamental approaches to safeguarding industrial pipe components against corrosion, ensuring optimal performance throughout their service life while maintaining safety and operational efficiency in demanding industrial environments.
Material Selection for Corrosion Resistance
The foundation of any effective corrosion prevention strategy begins with selecting appropriate materials for industrial pipe components. Different operating environments demand specific material properties to withstand unique corrosive challenges while maintaining structural integrity under varying pressures and temperatures.
High-Performance Stainless Steel Alloys
Stainless steel remains the gold standard for corrosion-resistant industrial pipe components, particularly in aggressive environments. The chromium content in grades like 304 and 316 forms a passive oxide layer that naturally resists oxidation. For more extreme conditions, super duplex stainless steels (UNS S32750) and nickel-based alloys like Inconel 625 offer exceptional resistance to pitting and stress corrosion cracking. These advanced alloys prove particularly valuable in offshore applications, chemical processing, and high-temperature steam systems where standard materials would rapidly deteriorate. The initial higher investment in premium alloys often proves cost-effective when considering extended service life and reduced maintenance requirements.
Protectively Treated Carbon Steel Solutions
While carbon steel lacks inherent corrosion resistance, various treatments transform it into a viable option for industrial pipe components. Hot-dip galvanizing creates a zinc barrier that sacrificially protects the base metal, ideal for outdoor applications and water distribution systems. For internal protection, fusion-bonded epoxy (FBE) coatings provide chemical resistance in oil and gas pipelines. Recent advancements in nano-ceramic coatings offer even greater protection with thinner applications, reducing flow restrictions while maintaining corrosion resistance. These treated carbon steel solutions deliver economic advantages without compromising performance in moderately corrosive environments.
Non-Metallic and Composite Alternatives
In highly corrosive applications where metal pipes face inevitable degradation, engineered plastics and composites present innovative solutions. Fiberglass-reinforced epoxy (GRE) pipes demonstrate remarkable chemical resistance in acid processing plants, while polyvinylidene fluoride (PVDF) components excel in semiconductor manufacturing where ultra-pure fluids are essential. For underground applications, high-density polyethylene (HDPE) pipes resist both chemical and electrochemical corrosion while offering flexibility that accommodates ground movement. These non-metallic industrial pipe components often outperform traditional metals in specific applications while reducing weight and installation costs.
Advanced Protective Coatings and Linings
Beyond material selection, secondary protection systems provide an additional defense layer for industrial pipe components operating in corrosive environments. These technologies create physical and electrochemical barriers that significantly extend service life while maintaining operational efficiency.
Multi-Layer Coating Systems
Modern coating technologies for industrial pipe components have evolved far beyond simple paint applications. Three-layer polyolefin systems combine epoxy primers with adhesive layers and polypropylene topcoats, creating nearly impermeable barriers for buried pipelines. For high-temperature applications, silicone-modified coatings maintain integrity at temperatures exceeding 400°C while resisting chemical attack. The latest developments in graphene-enhanced coatings demonstrate unprecedented barrier properties with reduced thickness, potentially revolutionizing corrosion protection for industrial pipe components in the coming decade.
Cathodic Protection Technologies
This electrochemical approach represents one of the most effective methods for protecting buried or submerged industrial pipe components. Impressed current cathodic protection (ICCP) systems use rectifiers to maintain a protective electrical potential, while galvanic anode systems employ sacrificial metals like magnesium or zinc. Modern monitoring systems integrate remote sensors and IoT technology to optimize protection levels and alert operators to any system deficiencies. These systems prove particularly valuable for cross-country pipelines, marine structures, and storage tank bottoms where external corrosion poses significant risks.
Internal Lining Solutions
The interior surfaces of industrial pipe components often face aggressive media that external coatings cannot address. Glass-flake reinforced linings provide exceptional abrasion and chemical resistance for slurry transport systems, while polyurethane linings offer flexibility for pipes experiencing thermal cycling. For water systems, cement mortar linings not only prevent corrosion but also maintain water quality by preventing metal leaching. Recent innovations in spray-applied ceramic linings demonstrate remarkable durability in refinery applications where both corrosion and erosion present challenges.
Proactive Maintenance and Monitoring Strategies
Even with premium materials and advanced coatings, industrial pipe components require systematic monitoring and maintenance to ensure long-term corrosion resistance. Implementing comprehensive inspection and intervention protocols can identify potential issues before they escalate into failures.
Non-Destructive Testing Techniques
Modern inspection methods allow thorough assessment of industrial pipe components without disrupting operations. Pulsed eddy current testing can detect wall thinning through insulation, while phased array ultrasonics provides detailed corrosion mapping. Long-range ultrasonic testing (LRUT) enables screening of hundreds of meters of pipe from a single test point, ideal for inaccessible pipelines. Advanced robotic crawlers equipped with multiple sensors can navigate complex piping systems, providing comprehensive condition assessments without requiring system shutdowns.
Corrosion Monitoring Systems
Permanent monitoring installations provide real-time data on corrosion rates within industrial pipe components. Electrical resistance probes measure metal loss directly, while linear polarization resistance (LPR) techniques assess active corrosion processes. Coupon racks allow periodic weight-loss measurements for trend analysis. Modern systems integrate wireless data transmission, enabling remote monitoring across multiple facilities. These systems not only detect active corrosion but also validate the effectiveness of corrosion prevention measures, allowing for timely adjustments to protection strategies.
Preventive Maintenance Protocols
Establishing systematic maintenance routines significantly extends the service life of industrial pipe components. Regular cleaning prevents under-deposit corrosion, while proper insulation maintenance avoids corrosion under insulation (CUI). Hydrotesting protocols should include corrosion inhibitor additives when testing new installations. For critical systems, risk-based inspection (RBI) programs prioritize resources toward components with the highest consequence of failure. Digital twin technology now enables virtual simulations of corrosion progression, allowing predictive maintenance scheduling before actual damage occurs.
Conclusion
Effective corrosion prevention in industrial pipe components requires a holistic approach combining material science, protective technologies, and vigilant maintenance. By implementing these strategies, industries can significantly extend asset lifecycles, reduce unplanned downtime, and maintain operational safety. The continuous advancement in corrosion-resistant materials, smart coatings, and predictive monitoring technologies promises even greater protection capabilities in the future, ensuring industrial piping systems meet increasingly demanding performance requirements.
Partner with HEBEI RAYOUNG for Corrosion-Resistant Solutions
At HEBEI RAYOUNG PIPELINE TECHNOLOGY CO., LTD, we engineer industrial pipe components that withstand the test of time and the harshest environments. Our ISO 9001:2015 certified manufacturing processes deliver buttweld fittings, flanges, and piping systems with exceptional corrosion resistance for global industrial applications. From carbon steel to specialty alloys, our solutions combine material excellence with precision engineering—ensuring reliable performance in your most critical systems.
Discover how our corrosion-resistant piping solutions can enhance your operations. Contact our technical team today at info@hb-steel.com for customized recommendations and project support.
References
1. Fontana, M.G. Corrosion Engineering, 3rd Edition. McGraw-Hill Education, 2005.
2. Roberge, P.R. Corrosion Inspection and Monitoring. Wiley, 2007.
3. Schweitzer, P.A. Corrosion Resistance Tables, 5th Edition. CRC Press, 2004.
4. ASM Handbook, Volume 13C: Corrosion: Environments and Industries. ASM International, 2006.
5. Trethewey, K.R. & Chamberlain, J. Corrosion for Science and Engineering, 2nd Edition. Pearson, 1995.
6. Baeckmann, W.v. Cathodic Corrosion Protection. Gulf Professional Publishing, 1997.
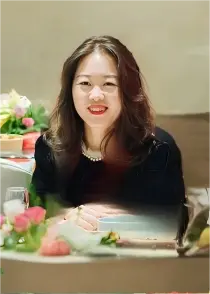
Need a quote? Want to see samples? Just say hello. We’re friendly. We’re fast. And we’re ready when you are.
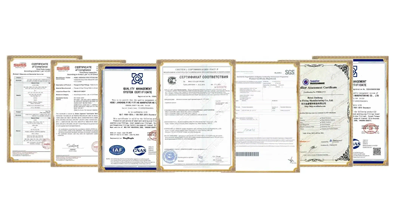
Welcome to RAYOUNG – Strong Pipes, Stronger Promise
Popular Blogs