Pipe Flanges: Types, Styles & Applications
Pipe flanges serve as critical connection points in piping systems across industries, enabling secure joining of pipes, valves, pumps, and other equipment while allowing for maintenance access. These circular discs with evenly spaced bolt holes come in various materials, pressure ratings, and face types to accommodate different system requirements. From petrochemical plants to water treatment facilities, proper flange selection ensures leak-proof connections that withstand operational pressures and environmental conditions. This guide explores the major categories of pipe flanges, their distinctive features, and how to match them with specific applications for optimal performance and longevity in industrial piping systems.
Pipe Flange Types That Are Common
Understanding different flange types is essential for selecting the right connection solution for specific pressure, temperature, and maintenance requirements in piping systems.
Weld Neck Flanges for High-Pressure Systems
Weld neck flanges feature a long tapered hub that provides reinforcement in high-stress applications, making them ideal for extreme pressure and temperature conditions. The smooth transition from flange thickness to pipe wall thickness reduces stress concentration, while the butt-weld connection ensures maximum strength. These pipe flanges are particularly valuable in oil and gas pipelines, power generation plants, and chemical processing systems where integrity under cyclic loading is critical. Their design allows for easy radiographic inspection of the weld joint, an important consideration in regulated industries requiring full penetration welds.
Slip-On Flanges for Cost-Effective Installation
Slip-on pipe flanges offer installation advantages with their lower initial cost and simpler welding requirements compared to weld neck varieties. The flange slides over the pipe and requires fillet welding on both the inside and outside, making them popular for low-pressure applications like water distribution and HVAC systems. While not suitable for severe service conditions, their ease of alignment proves beneficial during piping modifications or expansions. Many engineers specify slip-on flanges for systems operating below 300 psi and at moderate temperatures where the reduced material cost provides significant savings without compromising safety.
Socket Weld Flanges for Small-Bore Piping
Socket weld pipe flanges provide an excellent solution for small diameter high-pressure piping systems typically found in instrumentation lines and sample points. The pipe inserts into the socket and is welded around the top, creating a smooth bore that minimizes turbulence and pressure drop. These compact flanges offer greater strength than threaded alternatives while maintaining accessibility for maintenance. Their design makes them particularly suitable for chemical and pharmaceutical applications where cleanliness and leak prevention are paramount, though they're generally limited to pipe sizes below NPS 4 due to welding constraints.
Specialized Flange Styles and Configurations
Beyond basic types, specialized flange designs address unique system requirements and challenging operating environments.
Lap Joint Flanges for Systems Requiring Frequent Disassembly
Lap joint pipe flanges combine with stub ends to create systems that allow easy alignment and repeated disassembly without damaging the flange faces. This design proves invaluable in food processing, pharmaceutical, and chemical industries where regular cleaning and inspection are necessary. The flange itself rotates freely around the stub end, simplifying bolt hole alignment during reassembly. While not suitable for high-pressure applications, their cost-effectiveness in systems requiring maintenance makes them a preferred choice for many plant engineers working with corrosive media or sanitary requirements.
Threaded Flanges for Non-Welded Connections
Threaded pipe flanges provide a practical solution when welding isn't possible or desirable, particularly in explosive environments or for certain maintenance scenarios. These flanges screw onto the pipe's external threads, eliminating the need for hot work permits in hazardous areas. They find extensive use in fuel gas systems, compressed air lines, and certain water services where system modifications might be anticipated. However, engineers must consider potential leakage paths along the threads and typically limit their use to low-pressure applications below 300 psi. Proper thread sealing compounds and careful installation are essential for reliable performance.
Blind Flanges for System Isolation and Testing
Blind pipe flanges serve as removable closures in piping systems, allowing for future expansion, maintenance access, or pressure testing. These solid discs without a center hole withstand full system pressure when properly bolted, making them critical components during hydrotesting and system commissioning. In process plants, they isolate equipment for maintenance while maintaining the integrity of the overall system. Special variants include spectacle blinds (combination of blind and spacer) for permanent installation in systems requiring periodic isolation, demonstrating the versatility of these essential piping components.
Flange Applications Across Industries
Proper flange selection varies significantly by industry based on media, pressure, temperature, and regulatory requirements.
Oil and Gas Pipeline Flanges
The energy sector demands robust pipe flanges capable of withstanding extreme pressures, temperatures, and environmental conditions. ANSI B16.5 Class 1500 and 2500 weld neck flanges dominate high-pressure transmission lines, while ring-type joint (RTJ) faces provide metal-to-metal seals for critical wellhead applications. Offshore platforms often specify compact flange designs with enhanced corrosion protection to combat saltwater exposure. Recent advancements include integrally reinforced flanges for arctic conditions where material toughness at low temperatures becomes paramount for safety and reliability.
Chemical Processing Flange Solutions
Chemical plants require pipe flanges that resist aggressive media while maintaining seal integrity. Alloy materials like Hastelloy and titanium flanges handle corrosive fluids, while PTFE-lined flanges prevent product contamination. Raised face flanges with spiral wound gaskets are standard for most process piping, with special attention given to bolt loading to prevent crevice corrosion. Many facilities implement controlled bolting procedures using hydraulic tensioners to ensure uniform gasket compression, particularly when handling hazardous or toxic chemicals where leaks could have severe consequences.
Water and Wastewater Treatment Applications
Municipal water systems typically utilize ANSI B16.1 cast iron pipe flanges for large diameter transmission mains, while ductile iron flanges handle higher pressures in pumping stations. Rubber gasket joints with grooved flanges simplify installation in tight spaces common in treatment plants. For seawater desalination plants, super duplex stainless steel flanges provide the necessary corrosion resistance against chlorides. Engineers increasingly specify restrained joint flanges in areas prone to seismic activity, where maintaining pipeline integrity during ground movement is essential for public safety and system reliability.
Conclusion
Selecting appropriate pipe flanges requires careful consideration of pressure ratings, material compatibility, face types, and industry-specific requirements. From standard weld neck designs to specialized lap joint configurations, each flange type serves distinct purposes in creating reliable, maintainable piping systems. Understanding these variations ensures optimal performance, safety, and cost-effectiveness across diverse industrial applications.
HEBEI RAYOUNG PIPELINE: Your Trusted Partner for Premium Pipe Flanges
HEBEI RAYOUNG PIPELINE TECHNOLOGY CO., LTD manufactures high-quality pipe flanges that meet international standards including ANSI, ASME, and DIN specifications. Our ISO 9001:2015 certified production facility delivers reliable flange solutions for oil & gas, chemical processing, water treatment, and power generation applications. With GOST-R and SGS certifications ensuring export compliance, we provide buttweld, slip-on, blind, and specialty flanges in carbon steel, stainless steel, and alloy materials.
Contact our technical experts today at info@hb-steel.com to discuss your project requirements and discover how our flange solutions can enhance your piping system's performance and longevity.
References
1. ASME B16.5 - Pipe Flanges and Flanged Fittings
2. ASME B16.47 - Large Diameter Steel Flanges
3. API 6A - Specification for Wellhead and Christmas Tree Equipment
4. MSS SP-44 - Steel Pipeline Flanges
5. EN 1092-1 - Flanges and their joints
6. ASME Boiler and Pressure Vessel Code, Section VIII - Pressure Vessels
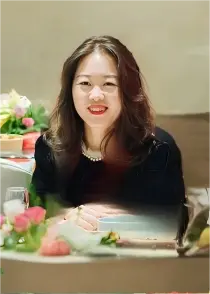
Need a quote? Want to see samples? Just say hello. We’re friendly. We’re fast. And we’re ready when you are.
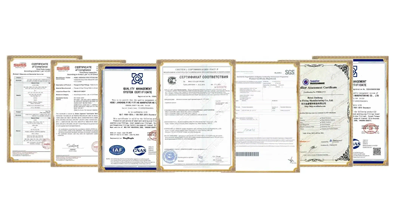
Welcome to RAYOUNG – Strong Pipes, Stronger Promise
Popular Blogs