How Does a Pipe Flange Work in a Plumbing System?
Pipe flanges serve as critical connection points in plumbing systems, providing secure, leak-proof joints between pipes, valves, and other components. Steel pipe flanges are particularly valued for their strength and durability in both residential and industrial applications. These circular fittings with evenly spaced bolt holes create a tight seal when compressed with gaskets, allowing for easy assembly, disassembly, and maintenance of piping networks. In plumbing systems, flanges enable directional changes, equipment connections, and system expansions while withstanding internal pressures and external stresses. Their standardized designs ensure compatibility across different manufacturers and simplify replacement procedures. This article will explore the mechanics, types, and proper installation techniques that make steel pipe flanges indispensable in modern plumbing infrastructure.
The Fundamental Mechanics of Flange Connections
Creating Pressure-Tight Seals in Piping Systems
The primary function of steel pipe flanges in plumbing systems is to establish reliable, pressure-resistant connections between pipe sections. When two flanges are aligned and bolted together with a gasket in between, they form a mechanical joint that can withstand significant internal pressure. The flange faces are machined to precise smoothness standards (typically Ra 3.2-6.3 μm) to ensure optimal gasket contact. As the bolts are tightened in a star pattern, the gasket material flows into microscopic imperfections on the flange faces, creating a custom-fit seal. Steel pipe flanges maintain this seal through thermal cycling and pressure fluctuations due to their high rigidity and bolt load retention. The number and size of bolts increase with flange diameter and pressure class, distributing the clamping force evenly around the circumference.
Facilitating System Assembly and Maintenance
Unlike permanent welded connections, steel pipe flanges provide practical access points within plumbing systems. This modular design allows for straightforward installation of valves, pumps, and other equipment by simply bolting them between flanges. During maintenance or repairs, technicians can disconnect specific sections without cutting pipes, significantly reducing downtime. The raised face on most steel pipe flanges (typically 1/16" for 150# and 300# classes) helps position and compress the gasket properly. Larger plumbing systems often use flanges at strategic intervals to create manageable segments for testing and commissioning. This accessibility makes steel pipe flanges particularly valuable in complex industrial plumbing networks where regular inspection and component replacement are necessary.
Accommodating System Movements and Stresses
Properly installed steel pipe flanges can accommodate certain degrees of pipe movement and vibration without leaking. The flexibility of the gasket material absorbs minor misalignments and thermal expansion/contraction movements in the piping system. In high-vibration applications, flanges with ring-type joints (RTJ) provide superior performance by using metal-to-metal sealing. Steel pipe flanges also help distribute mechanical stresses at connection points, preventing localized fatigue in the pipe wall. For underground plumbing systems, flanges with protective coatings resist soil stresses and corrosion while maintaining connection integrity. The robustness of steel pipe flanges makes them suitable for handling both static and dynamic loads in diverse plumbing applications.
Types of Flanges Used in Plumbing Systems
Slip-On Flanges for General Plumbing Applications
Slip-on steel pipe flanges are among the most commonly used types in residential and commercial plumbing systems due to their ease of installation. These flanges slide over the pipe end and are secured with two fillet welds (inside and outside the flange), making them more economical to install than weld neck flanges. Their compact design works well in space-constrained plumbing chases and mechanical rooms. Slip-on steel pipe flanges are typically specified for low to medium pressure applications (up to ASME Class 300) in water supply and drainage systems. The smooth bore transition minimizes turbulence and pressure drop, which is particularly important in plumbing systems where flow efficiency affects performance. Proper welding techniques are crucial to prevent distortion that could compromise the flange face flatness.
Threaded Flanges for Small-Diameter Plumbing Connections
Threaded steel pipe flanges provide a practical solution for small-bore plumbing connections (typically NPS 2" and below) where welding isn't feasible or desired. These flanges feature internal threads that match standard pipe threads, allowing for screw-on assembly without specialized tools. They're commonly used in water supply lines, gas piping, and chemical feed systems where occasional disassembly may be required. Threaded steel pipe flanges eliminate welding costs and heat-affected zone concerns in sensitive applications. However, proper thread sealing using PTFE tape or thread compounds is essential to prevent leaks. These flanges require careful installation to avoid cross-threading and should not be used in systems with significant thermal cycling, as differential expansion can loosen the threaded connection over time.
Blind Flanges for System Termination and Testing
Blind steel pipe flanges play several important roles in plumbing system installation and maintenance. These solid discs are used to seal off the ends of piping systems permanently or temporarily during pressure testing. In large plumbing networks, blind flanges allow for future system expansion by providing capped connection points. They're essential for isolating sections of the plumbing system during repairs or modifications without draining the entire system. Blind steel pipe flanges withstand full system pressure when properly installed and are available in all standard pressure classes to match the connected piping. Their simple yet robust design makes them reliable termination points in both vertical and horizontal plumbing runs, from basement mains to rooftop equipment connections.
Proper Installation and Maintenance Practices
Flange Alignment and Bolt Tightening Procedures
Correct installation begins with precise alignment of steel pipe flanges before bolting. Misalignment exceeding 1/8" per foot of pipe diameter can cause gasket failure and leakage. Using alignment pins or flange spreaders helps achieve parallel flange faces and concentric bolt holes. The bolting sequence should follow a star or crisscross pattern to apply even compression to the gasket. For plumbing systems, torque values should be calculated based on bolt material, gasket type, and service conditions rather than using generic values. Progressive tightening in three stages (30%, 70%, and 100% of final torque) allows the gasket to seat properly. Steel pipe flanges in plumbing applications often require retorquing after the first few thermal cycles as gasket materials compress and relax. Digital torque wrenches provide the most accurate and repeatable results for consistent joint integrity.
Gasket Selection for Plumbing System Requirements
The gasket is the critical sealing element between steel pipe flanges, and proper selection depends on the plumbing system's media, pressure, and temperature. Non-asbestos fiber gaskets work well for cold water systems, while rubber-faced corrugated metal gaskets handle hot water and steam applications. Full-face gaskets (covering the entire flange face) are common in plumbing systems, while ring-type gaskets are used for higher pressure applications. Gasket thickness should be appropriate for the flange face finish - typically 1/16" for standard raised face steel pipe flanges. For potable water systems, NSF-approved gasket materials prevent contamination concerns. Proper gasket installation includes cleaning flange faces, ensuring the gasket is centered, and avoiding over-compression that could damage the gasket material.
Corrosion Protection and Long-Term Maintenance
Steel pipe flanges in plumbing systems require protection against both internal and external corrosion. Galvanized or epoxy-coated flanges extend service life in humid environments and underground installations. Dielectric unions or isolation kits prevent galvanic corrosion when connecting dissimilar metals in the plumbing system. Regular inspection should check for signs of leakage, bolt corrosion, or gasket degradation. In areas with aggressive water chemistry, more frequent inspection intervals may be necessary. Maintaining proper bolt loads is crucial - undertorqued bolts allow leakage while overtorqued bolts can damage flanges or gaskets. For critical plumbing systems, implementing a flange management program that documents installation details, torque values, and maintenance history helps optimize long-term performance of steel pipe flanges.
Conclusion
Steel pipe flanges serve as versatile, reliable connection points in plumbing systems by combining mechanical strength with practical serviceability. Their standardized designs and proper installation techniques ensure leak-free performance across residential, commercial, and industrial applications. Understanding flange types, selection criteria, and maintenance requirements enables plumbing professionals to build durable, efficient piping networks.
HEBEI RAYOUNG PIPELINE: Trusted Flange Solutions for Your Plumbing Projects
At HEBEI RAYOUNG PIPELINE TECHNOLOGY CO., LTD, we manufacture premium steel pipe flanges that meet rigorous international standards for plumbing and industrial applications. Our ISO 9001:2015 certified production processes ensure consistent quality, dimensional accuracy, and reliable performance in all your piping projects. From standard ASME B16.5 flanges to custom solutions, our product range combines engineering excellence with practical innovation. Contact our technical team today at info@hb-steel.com to discuss how our flange products can enhance your plumbing system's reliability and longevity.
References
1. ASME B16.1 - Cast Iron Pipe Flanges and Flanged Fittings
2. ASTM A105/A105M - Standard Specification for Carbon Steel Forgings for Piping Applications
3. AWWA C110 - Ductile-Iron and Gray-Iron Fittings
4. ASME B31.9 - Building Services Piping
5. MSS SP-43 - Standard Practice for Lightweight Stainless Steel Pipe Flanges
6. NSF/ANSI 61 - Drinking Water System Components - Health Effects
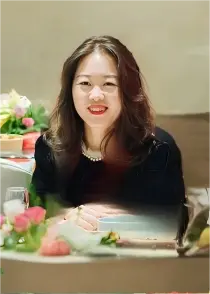
Need a quote? Want to see samples? Just say hello. We’re friendly. We’re fast. And we’re ready when you are.
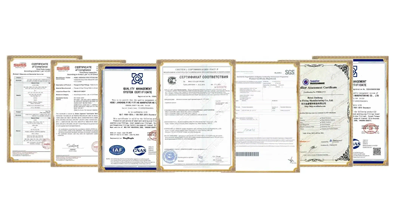
Welcome to RAYOUNG – Strong Pipes, Stronger Promise
Popular Blogs